A span clamp is a device used to secure conductors in place between two adjacent towers. A span clamp is also known as a mid-span clamp or a suspension clamp. Its main purpose is to provide mechanical support and maintain the proper sag. This is to ensure the integrity and reliability of the transmission lines by preventing excessive movement. The span clamp has gripping mechanisms to secure the cable in place. They are from durable materials designed to withstand the forces on transmission lines. These materials include stainless steel or aluminum. Span clamps install along the span of the line to distribute the load and maintain the desired tension. Use of span clamps allows for the attachment of various accessories. This is depending on specific requirements of the line. These accessories include vibration dampers, spacer dampers and conductor splice.
Features of span clamp
Span clamps have several features that help ensure their effectiveness and reliability on transmission lines. These features contribute to the safe and efficient operation of the power systems. The following are the various features of span clamps.
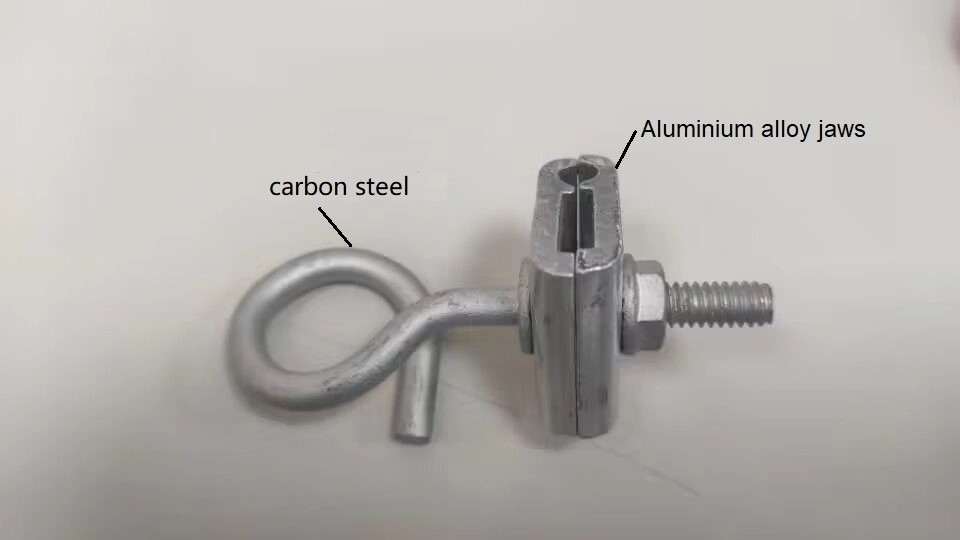
- Material – span clamps are from materials with high strength materials. These include aluminum or steel. these materials help to withstand the mechanical stresses and environmental conditions.
- Adjustability – the clamps are adjustable to hold various conductor sizes and to fine-tune the tension in the line. This is through the use of bolts, nuts or other mechanisms that allow for precise tightening.
- Insulation – span clamps have insulation materials to prevent electrical contact between the conductor and the clamp. this helps reduce the risk of electrical faults.
- Load capacity – they have ratings to ensure they can support the weight of the conductor and any extra accessories.
- Reliability – span clamps are reliable for long term performance with designs that reduce the risk of failure.
- Design – they have designs to grip the conductor without causing excessive wear. The design includes grooves, serrations or other features to prevent slippage.
- Corrosion resistance – span clamps have coatings to resist corrosion and extend the lifespan.
- Compatibility – the clamps are compatible with various types of conductors. This is including aluminum, copper or composite materials. They are available in different sizes or configurations to hold different conductor diameter and types.
- Installation – they also have designs to enhance easy installation with features that are simple, straightforward mechanisms.
How to select the best span clamp
Proper selection of the span clamp helps to ensure the safety and performance of the application. It involves considering several factors such as type, material and environmental conditions. Additionally, it is important to consult with industry professionals for guidance of the best span clamp for your application. The following are the factors to consider when selecting span clamps.
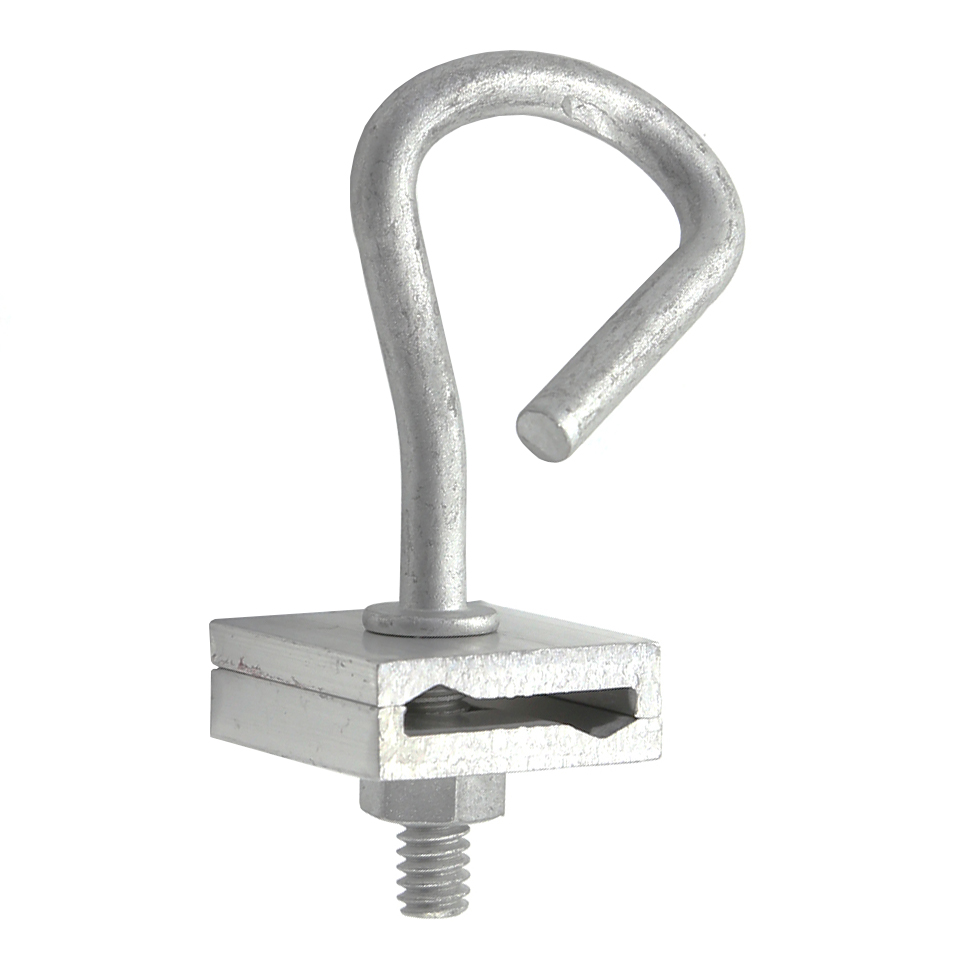
- Requirements – assess the specific needs of a power line project like voltage level, conductor types and the function of the clamp.
- Compatibility – assess the adjustability and compatibility of the clamp. Ensure that the span clamp is compatible with the conductor size and shape. It should have designs to securely hold and support the conductor without causing damage.
- Load ratings – assess the load capacity of the span clamp to ensure it can handle the expected mechanical loads. Consider factors such as winds, ice and weight of the extra accessories to install.
- Electrical requirements – consider the electrical conductivity requirements of the application. This is to provide good continuity and cut resistance.
- Environmental conditions – check the environmental conditions like humidity, salt spray or chemical exposure. This helps to select a clamp with resistance.
- Manufacturer reputation – select span clamps from manufacturers with a track record of product quality. Check requirements such as conductor compatibility, load capacity, material composition and corrosion resistance.
- Insulation needs – determine whether the insulation materials are necessary. They help to prevent electrical contact between the conductor and the clamp.
- Cost considerations – check the cost-effectiveness of different span clamp options. Consider factors such as initial purchase price, maintenance requirements and expected lifespan.
Installation guide for mid-span clamps
The installation process for span clamps should aim to ensure safe and effective connection. The process varies depending on the specific design of the clamp and the requirements of the application. Additionally, it is important to consult with professionals or refer to manufacturer’s installation instructions for guidance. The following is a general installation process for span clamps.
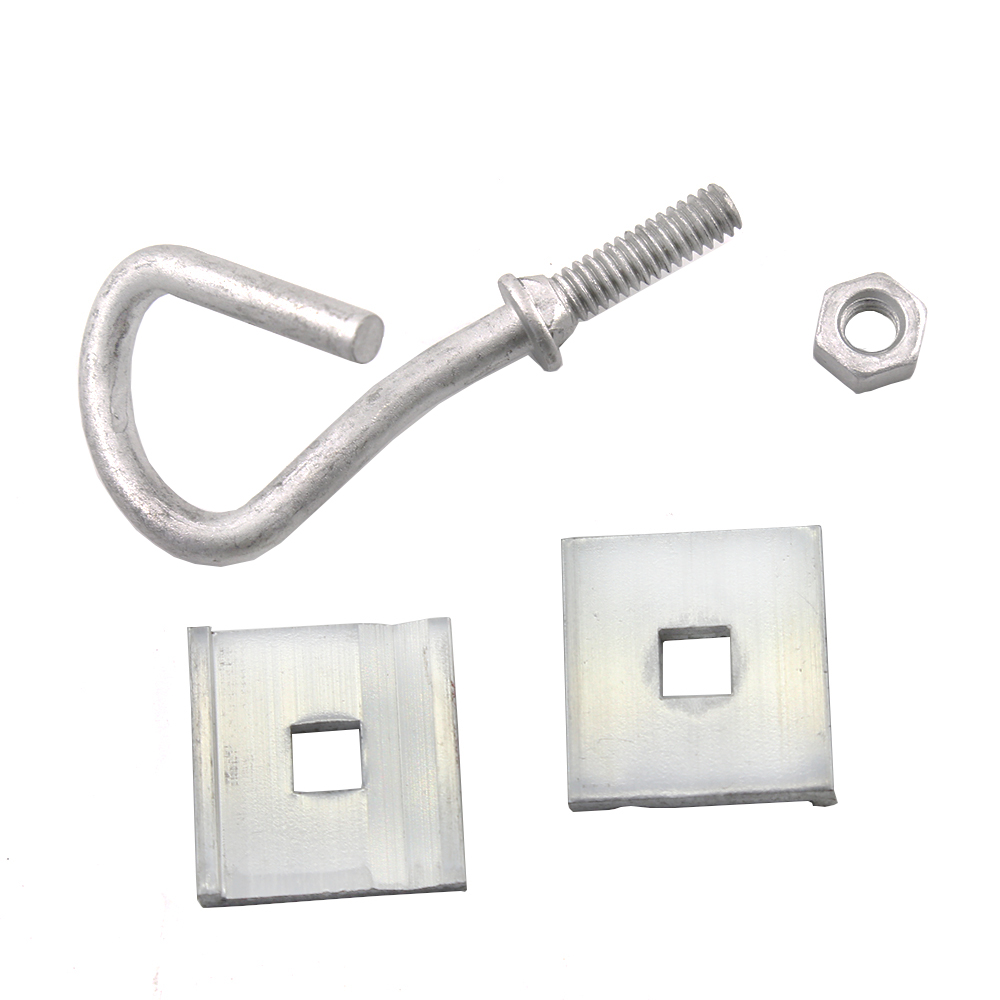
- Site assessment – check the power line span and identify the appropriate locations for installing the span clamp. You should also consider the length of the span, conductor type and size and the desired tension and sag parameters.
- Preparing the conductor – make sure the conductor is clean and free from contaminants that may affect the grip of the span.
- Span clamp positioning – Install the span clamps at the desired location along the power lines. This is where the spacing depends on the conductor type, size and sag requirements.
- Aligning the conductor – this is positioning the conductor within the gripping elements of the span clamp. Ensure that the conductor is at the center and aligned for optimal grip and performance.
- Tension adjustment – use the available change mechanism to fine-tune the tension in the conductor.
- Securing the clamp – secure the span clamp by tightening the bolts or fasteners provided. This is to ensure a secure and reliable connection.
- Inspection and testing – inspect the clamps to ensure they are securely fastened, aligned and free from defects. Conduct performance tests to ensure the clamps are functioning as intended.
- Documentation – keep records of the installation including location, date of installation and any adjustment made.
Safety inspection of span clamps
Span clamp inspection is important to ensure the integrity and reliability of overhead transmission lines. Safety inspections help to identify and address potential issues with span clamps. This is to maintain the integrity and reliability of the transmission line system. Also, it is important to conduct professional inspections once in a while. The following are the inspection practices for span clamps.
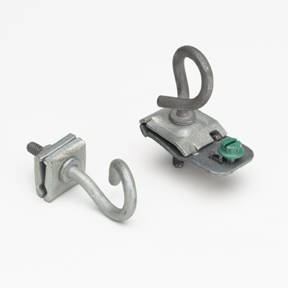
- Visual inspection – this is inspecting each span clamp along the transmission line. Check for signs of damage like cracks, dents, bends or deformation in the clamp body.
- Corrosion checks – examine the span clamps for signs of corrosion or rust on bolt heads, nuts and the clamps surfaces.
- Tightness – check the tightness of the bolts, nuts and other fasteners used to secure the span clamp. loose fasteners can cause the clamp to shift or become dislodged.
- Gripping surface inspection – check the gripping surfaces of the clamp looking for signs of wear, abrasion or indentations.
- Insulation check – inspect the insulating materials for signs of damage, deterioration or degradation.
- Alignment – check the alignment of the span clamp to ensure it is properly aligned and seated on the conductor.
- Load distribution – check the condition of the distribution components such as spacer dampers or vibration dampers.
Maintenance practices for mid-span clamps
Maintenance of span clamps helps to ensure the integrity and reliability of the transmission system. it also helps to ensure the continued performance and reliability of span clamps. This in turn helps to reduce the risk of failures and optimizing the lifespan of the transmission system. the following is a basic guide for maintenance of span clamps.
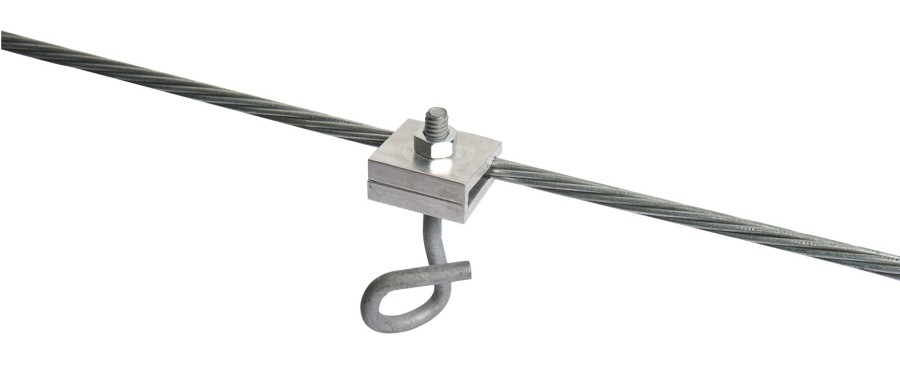
- Perform visual inspections to check for any signs of damage, corrosion or wear on the span clamp. Check for loose bolts, nuts or other components.
- Ensure the span clamp is properly aligned with the conductor and the support structure to prevent uneven stress distribution.
- Inspect the span clamp for signs of corrosion which can weaken the clamp and reduce the effectiveness. Apply corrosion-resistant coatings and replace corroded components as needed.
- Verify the tightness of all fasteners including bolts and nuts which can compromise the stability and load bearing capacity of the span clamp. use suitable tools to ensure the fasteners are tight to the recommended torque specifications.
- Inspect the insulating materials for any damage to ensure the materials maintain their integrity. Ensure the insulation remains intact and provides effective electrical insulation between the conductor.
- Periodically clean the span clamp to remove dirt and debris to ensure proper functioning.
- Follow the manufacturers recommendations for periodic lubrication to maintain smooth operation.
- Periodically check and adjust the tension following the manufacturers guidelines for proper adjustment procedures.
- After exposure to extreme environmental conditions, check the span clamps for signs of wear or corrosion.
- Inspect the damper for any signs of wear to ensure the damper remains effective in controlling vibrations.
- Maintain detailed records of inspections, maintenance activities and any repairs or replacements performed on span clamps.
Frequently asked questions
This is a hardware component used to secure conductor wires between two adjacent transmission poles. This helps maintain the proper sag and tension of the conductor.
Consider factors such as conductor type and size, expected loads, environmental conditions, adjustability, compatibility, load ratings and cost.
This is through implementing a comprehensive maintenance program, conducting regular inspections and addressing issues promptly, using corrosion-resistant materials and ensuring proper alignment and installation.