An insulated piercing clamp is also known as an IPC. It is an electrical connector used in power distribution systems. It helps connect service cables or secondary distribution lines to the main distribution feeder. The clamps provide safe, reliable and efficient connections between main feeders and service lines. IPCs has technical designs and features optimized to meet the requirements of power applications. This is to ensure ease of installation and long-term performance. It consists of a body made of durable and corrosion resistant materials. It also has a piercing design that penetrates the insulation of the main feeder cable. This is necessary to secure electrical connection without the need to strip the cable. Such clamps find use in various electrical and construction application.
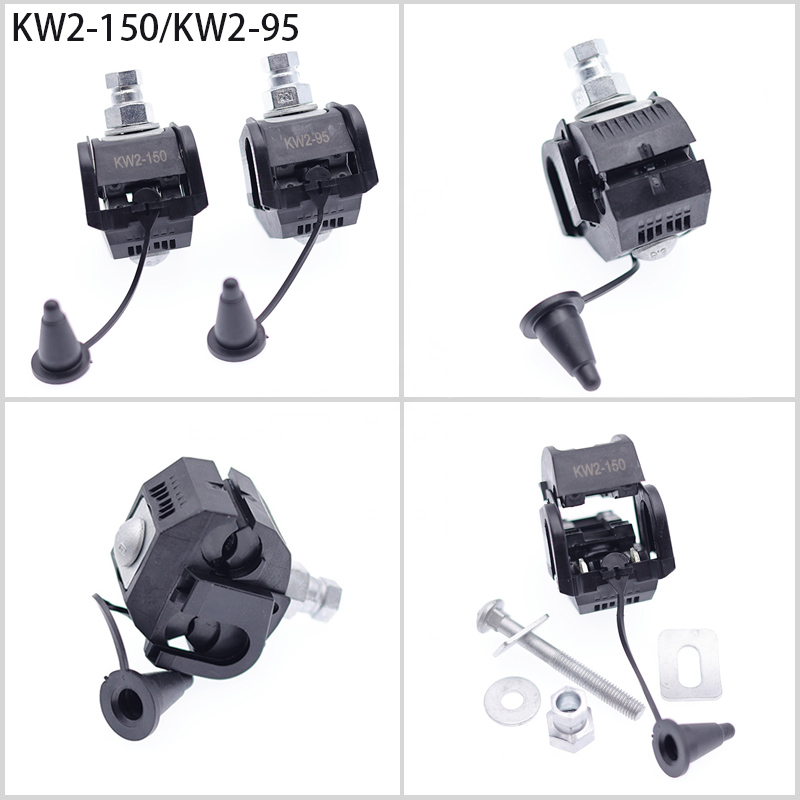
Types of insulated piercing clamp
There are various types of insulated piercing clamps that work in electrical installations. Each of these types have designs to meet specific needs of the application. Choosing the type of IPC depends on various factors. These include the application, conductor size, environmental conditions and installation requirements. The following are the common types of insulated piercing clamps.
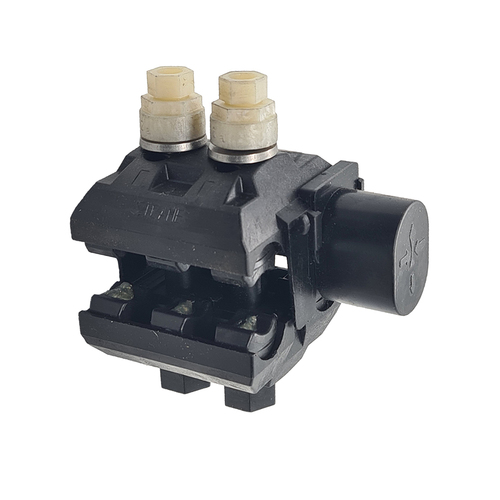
- Sleeve IPC – this helps in repairing damaged sections of overhead conductors. They feature sleeve designs that compress the damaged area. This is to provide insulation and structural support.
- Compression IPC – these types use a hydraulic tool to apply pressure and compress the clamp piercing the insulation. They provide a more uniform and consistent connection compared to bolted clamps.
- Tap insulated piercing connectors – the clamps connect service lines to transformers in distribution systems. They feature a tapping point and insulation suitable for connecting to transformer terminals.
- Branch-tap IPC – these create a branch connection from the main feeder line to a secondary distribution line. They feature a tapping point and insulation suitable for branching off from the main feeder.
- Wedge-based IPCs – these types use a wedge mechanism to drive the piercing teeth through the insulation. They are compact and lightweight which makes ideal for space-constrained application.
- Single-conductor IPC – this connects to a single conductor from the service line to the main feeder. It features a piercing mechanism and insulation suitable for a single conductor.
- Bolted IPC – these are most used type which feature a housing with a bolt and nut mechanism for tightening.
Factors influencing the material selection for IPC
Insulated piercing clamps are from various materials that depend on specific type of application. Common materials include thermoplastic, tinned copper, aluminum and high strength alloys. There are several factors that influence material selection for insulated piercing clamps. This is to help ensure optimal performance, durability and safety. Additionally, it is advisable to consult with industry professionals for guidance on the best material for your application. The following are the factors that influence the material for IPC.
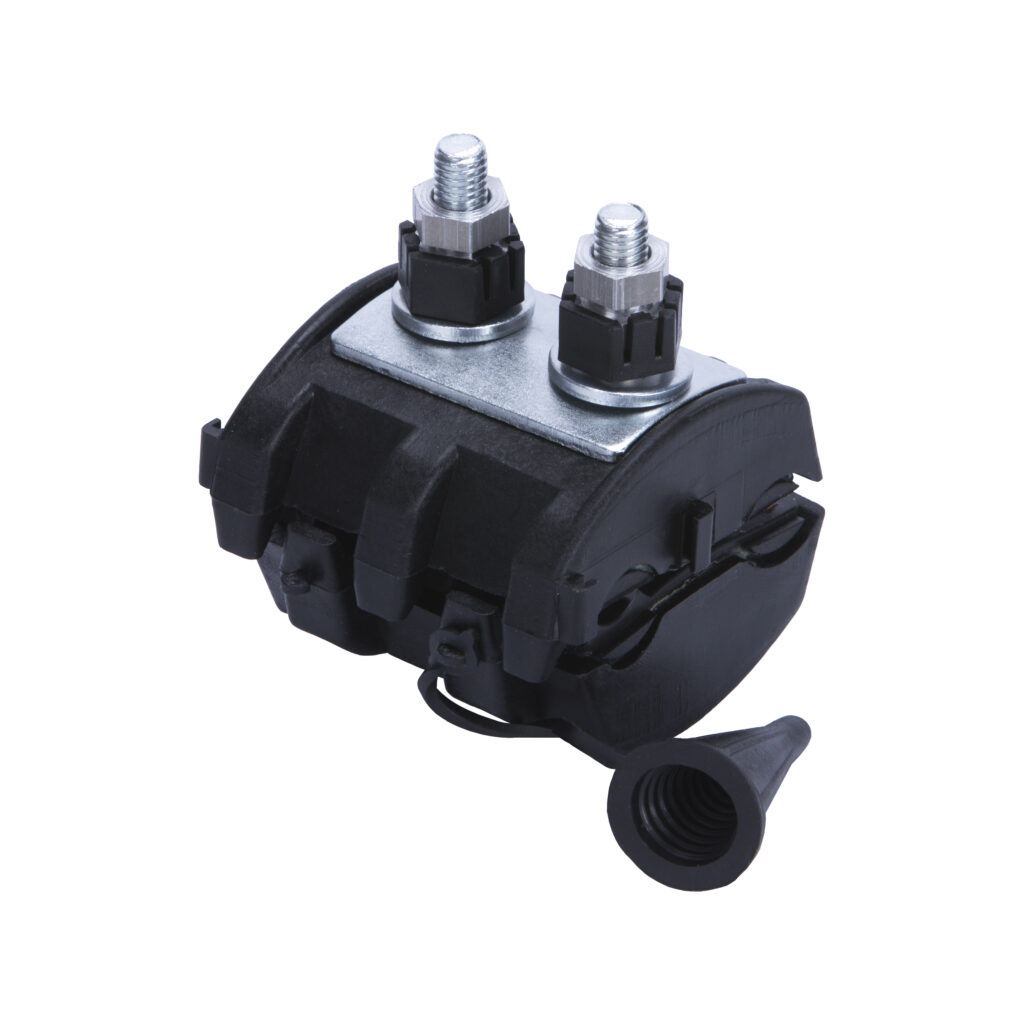
- Corrosion resistance – outdoor IPCs face factors like moisture, humidity and various corrosive agents. They thus need materials with excellent corrosion resistance. These includes aluminum alloys with coatings.
- Temperature resistance – materials with good temperature resistance properties work in cold to high heat environments. Aluminum alloys maintain the mechanical and electrical properties of the clamps.
- Weight – IPCs weight can affect the structural integrity and sag of the lines. lightweight materials such as aluminum alloys help reduce the weight of the clamp. this in turn maintains the adequate mechanical strength.
- Electrical conductivity – the IPC material should have high electrical conductivity. This is to reduce energy losses and ensure efficient power transmission. These materials include aluminum and copper.
- Mechanical strength – the clamps withstand Mechanical stresses such as tension, compression and bending. These materials include stainless steel or high strength aluminum alloys. They ensure the structural integrity of the clamp.
- Insulation properties – the material should have excellent dielectric properties for effective electrical insulation. It should also prevent electrical leakage or short circuits. Such materials include high density polyethylene or silicone rubber.
- Cost – manufacturers should strive to balance performance requirements with the cost of materials. This is to ensure the final product remains competitive in the market.
Cons of materials used for insulated piercing connectors
The materials for IPCs provide various advantages to applications. They also have challenges and limitations. Manufacturers should consider these limitations and balance them against the benefits of each material during design. Also, proper maintenance and installation practices help mitigate some of the cons to ensure the performance of the IPC. The following are the various limitations of materials for insulated piercing clamp.
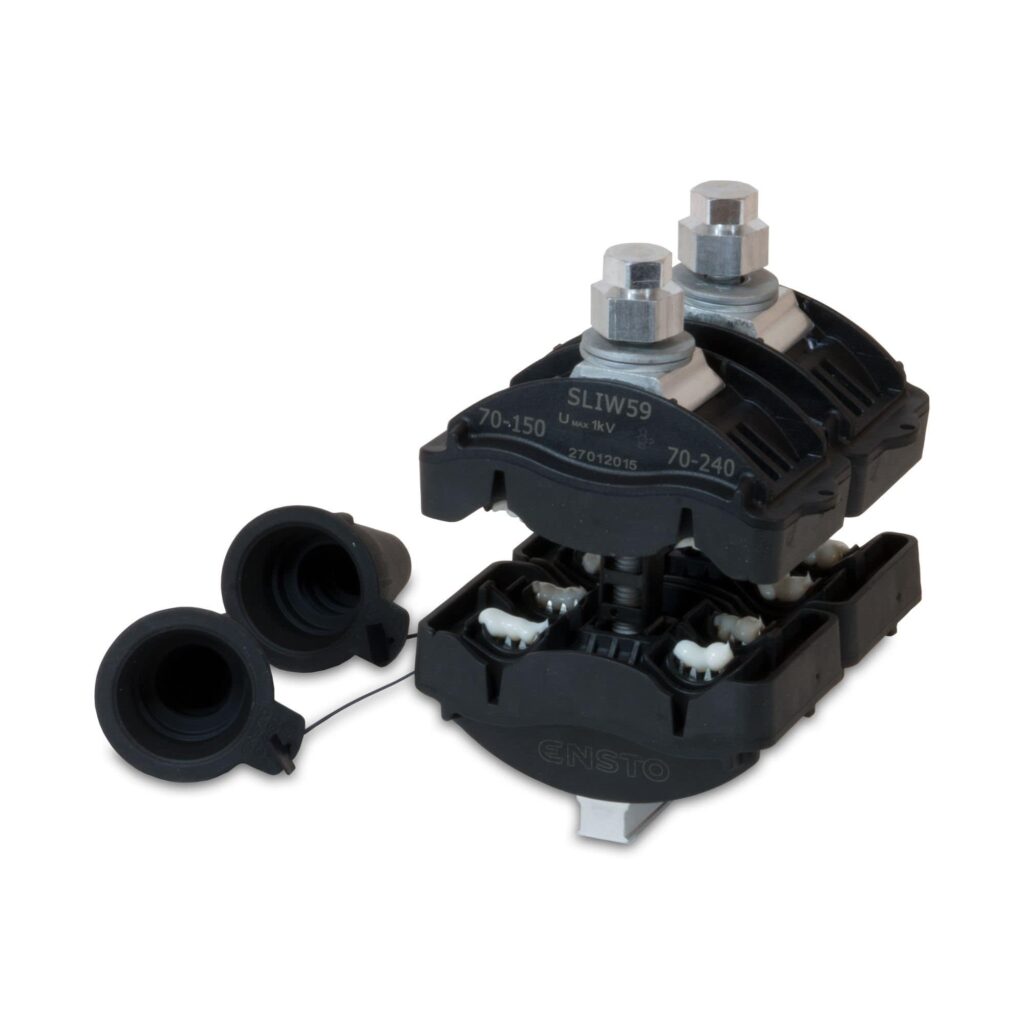
- Aluminum – this material has lower tensile strength compared to other metals like steel. This mainly affects mechanical durability. It is also susceptible to galvanic corrosion when in contact with dissimilar metals. They also have higher thermal expansion coefficient compared to steel. This can lead to dimensional changes.
- Stainless steel – these has higher material cost compared to aluminum which makes them more expensive. They also have greater weight compared to aluminum. It can increase transportation and installation challenges.
- Silicone rubber – they have limited temperature resistance compared to other insulating materials. They are also vulnerable to abrasion and physical damage especially in outdoor conditions.
- Copper – this has higher cost compared to aluminum which makes copper-based IPCs less cost effective. They are also heavier compared to aluminum which increases transportation and installation challenges.
- High density polyethylene (HDPE) – they have lower mechanical strength compared to metals. This affects their durability and load bearing capacity of the clamp. they are also susceptible to degradation from prolonged exposure to UV radiation. This may lead to brittleness and reduced insulation properties.
- Corrosion resistant coatings – coating may wea off leading to reduced corrosion protection. The application process can add complexity and cost to manufacturing. This affects the production expenses.
Technical specifications for insulated piercing clamp
Technical specifications for the IPC vary depending on factors such as the manufacturer, intended application and regional standards. The specifications provide valuable information for engineers, installers and users. They ensure the IPCs are properly selected, installed and operated safely and effectively. The following are the technical specifications related to insulated piercing clamp.
Type | equivalent Type | Mainline Section (mm2) | Branch Section (mm2) | Nominal Current (A) | Ooutline Size (mm) | Weight (g) | Piercing depth (mm) |
MT101 | JJC-1 | 1.5-2.5 | 1.5-10 | 55 | 27×41×62 | 55 | 1.5-2 |
MTEP | JJC-2 | 16-95 | 1.5-10 | 55 | 27×41×62 | 55 | 1-2 |
MT2-96 | JJCC-3 | 16-95 | 1-35(50) | 157 | 46×52×87 | 260 | 1.5-2 |
MT2-150 | JJC-4 | 50-150 | 6-36(50) | 157 | 45×52×87 | 162 | 1.5-2.5 |
MT3-95 | JJC-5 | 25-95 | 25-95 | 214 | 50×61×100 | 198 | 1.5-2 |
MT3-120 | JJC-5-1 | 16-120 | 16-120 | 214 | 50×61×100 | 198 | 1.5-2 |
- Voltage rating – the clamps should have ratings for specific voltage levels to ensure safe and reliable operation. Voltage ratings include low voltage, up to 600 volts and medium voltage e.g. 1 kV to 35kV.
- Insulation material – the insulation material used plays a crucial role in providing electrical insulation and environmental protection. Common materials include high density polyethylene, silicone rubber and various thermoplastics.
- Temperature rating – the clamps should withstand a wide range of temperatures in outdoor environments. The ratings specify the most and least temperatures at which the clamp can operate without compromise.
- Installation requirements – IPCs have specific installation requirements such as installation tools, torque values and procedures. They ensure proper installation and optimal performance of the clamp.
- Conductor size and compatibility – the clamps accommodate a range of conductor sizes which include the least and greatest conductor sizes.
- Current carrying capacity – the clamps have ratings for greatest current they can carry without overheating. Current carrying capacity depends on factors such as conductor size and material.
- Corrosion resistance – IPCs intended for outdoor use are often designed to resist corrosion from environmental factors. These include moisture, humidity and salt spray. The specifications may include information about the type of coating or material used to protect against corrosion.
- Mechanical strength – the clamps must have enough mechanical strength. This is to withstand mechanical stresses such as tension, compression and bending.
Frequently asked questions
An IPC is an electrical connector used in power distribution systems to connect service cables or secondary distribution lines to the main distribution feeder.
The main components of an IPC include a body made of durable materials, a piercing mechanism for making electrical connections and insulation. This is to prevent electrical leakage and fasteners for secure installation.
IPCs are from materials such as aluminum, copper, stainless-steel, high-density polyethylene, silicone rubber and corrosion resistant coatings.
Factors influencing material selection for IPCs include electrical conductivity, corrosion resistance, mechanical strength, temperature resistance and insulation properties.
The technical specifications of IPCs include size compatibility, voltage rating, current carrying capacity, insulation material, corrosion resistance, temperature rating and mechanical strength