An insulator pin is a component used to provide mechanical support and electrical insulation to conductors. It is a metal stud that securely mounts on the crossarm of a power pole. The main function of the insulator pin is to serve as an anchor point for attaching the insulator. The insulator pin acts as a support structure made of durable and weather resistant materials. The threaded end of the insulator pin allows for the secure attachment of the insulator to the crossarm. Insulator pin ensures a reliable connection between the electrical conductor and the support structure. Materials like steel and aluminum helps them to provide reliability in the extreme weather conditions in South America. Examples include spindle pin, straight pin, threaded pin, ball and socket pin and forked pin. They find use in applications such as transmission, telecommunication and industrial power lines.
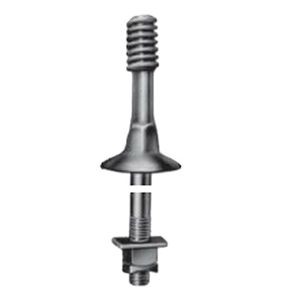
Key features of insulator pin
The insulator pin has various features that help to provide mechanical support. they also provide electrical insulation for conductors and insulators. The following are the common features of the insulator pin.
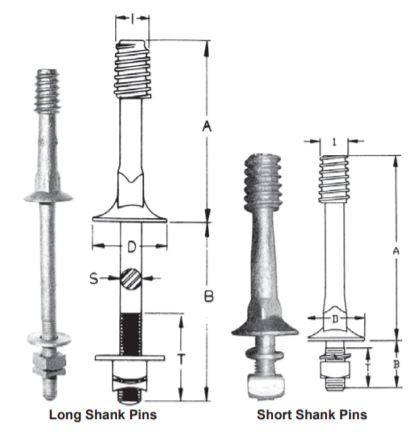
- Threaded design – this allows the insulator pins to securely attach to the crossarm. It also ensures a reliable and stable connection in areas prone to wind and other forces.
- Insulator attachment mechanisms – this includes mechanisms such as clevis pins or clamp tops. This helps to provide both stability and ease of installation.
- Corrosion resistance – they insulators should also be resistant to corrosion. This is to ensure they maintain the structural integrity.
- Ease of installation – they have features such as threaded ends or clevis attachments. They help to contribute to the ease of installation and reduce downtime.
- Pollution resistance – insulator pins should resist accumulation of contaminants on their surface.
- Material – they are from materials that are durable and weather resistance. This is to provide mechanical strength.
- Grooved end – this end helps to ensure the attachment of insulators to provide a secure fit for the insulator.
- High mechanical strength – withstanding the weight of conductors, wind loads and other environmental factors ensures the longevity of the pin.
- Voltage compatibility – the insulator pins should meet the specific voltage requirements of the power lines.
Selection and installation of insulator pin
Proper selection if the insulator pin ensures the optimal performance and reliability of the application. It includes considering various factors. These include voltage class, mechanical strength, material, threaded end, environmental conditions and cost considerations. The installation is a critical process requiring careful attention and expertise. This is to ensure proper functionality and safety. The following is a step-by-step installation guideline for the insulator pin.
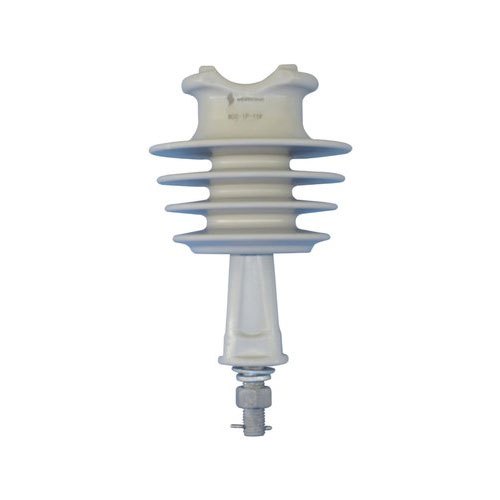
- Preparation – gather all the necessary tools and equipment required for the installation. This is including safety equipment, wrenches, insulator pin, insulator and mounting hardware. Ensure the power line is de-energized and properly rounded before starting.
- Positioning – position the insulator pin on the crossarm at the desired location. Ensure the threaded end of the insulator aligns properly.
- Attachment to crossarm – use suitable wrench to securely attach it to the crossarm. Ensue the insulator pin is tightly secured to prevent movement.
- Insulator attachment – use recommended hardware to attach the insulator securely.
- Insulator placement – place the insulator over the insulator pin and ensure it fits onto the grooved clevis end.
- Securing hardware – use the suitable nuts and washers to secure the insulator to the insulator pin. Tighten them to the specified torque levels to ensure a secure and stable connection.
- Inspection – conduct visual inspection to ensure the insulator pin and insulator are securely attached and properly aligned.
- Energization – after installation, re-energize the power line following the established procedures.
- Documentation – maintain records of the installation including torque values used and dates.
Maintenance and inspection of insulator pin
Regular maintenance and inspection of insulator pin ensures the continued reliability and safety of power systems. It also helps to identify and address potential issues to prevent failures and power outages. Additionally, it is advisable to consult with qualified professionals for further assessment and corrective action. The following is a basic guide for the maintenance and inspection of insulator pin.
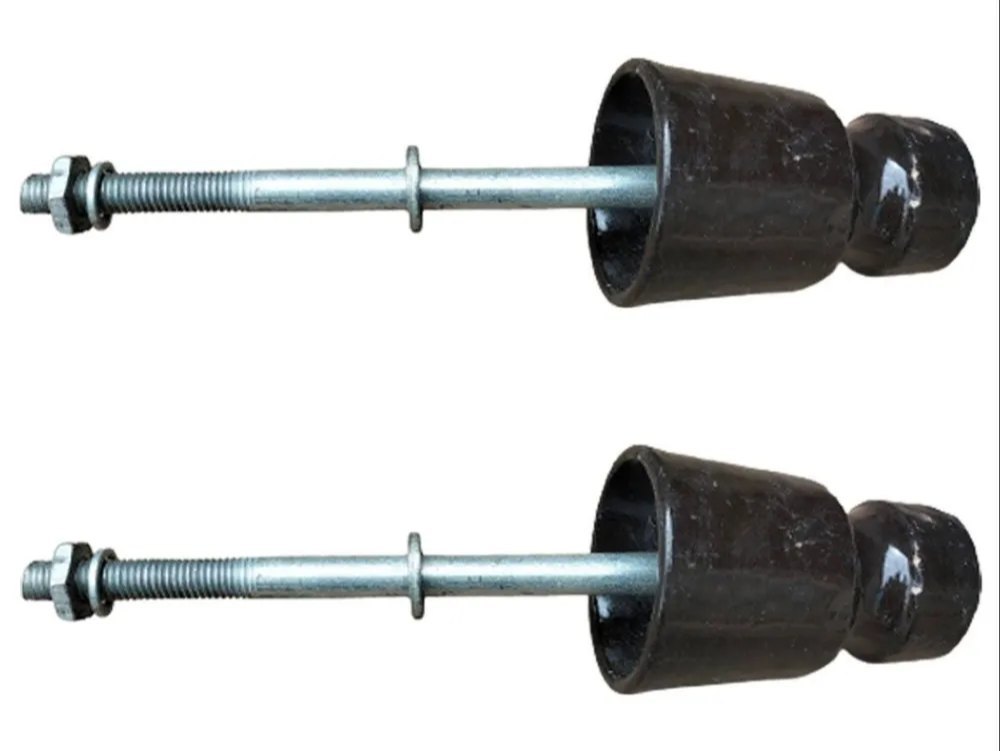
- Regularly inspect insulator pins for visible signs of damage, wear or corrosion. Check for cracks, chips or any deformities in the insulator pin.
- Ensure the insulator pins are free from dirt, dust and contaminants. Clean the insulator pins to prevent pollution related flashovers.
- Confirm secure attachment of the insulator pins to the cross arm. Check the tightness of the nuts and bolts to ensure they meet the specified torque values.
- Verify the proper alignment of the insulator pins and ensure they securely fit into the grooved end.
- Apply corrosion resistant coatings to protect against corrosion especially in corrosive environments.
- Check and re-tighten nuts and bolts to maintain the specified torque values. Use a toque wrench to ensure accurate torque application.
- Inspect the insulators for any signs of cracks, contamination or damage. replace damaged insulators accordingly.
- Consider the environmental conditions of the installation site and adapt maintenance practices accordingly.
- Perform ultrasonic testing to detect any internal defects in the insulator pins. This is non destructive testing method identifies issues not visible during visual inspections.
- Maintain detailed records of all inspections and maintenance activities. Document any corrective actions taken.
Comparative analysis of insulator pin in South America
Conducting a comparative analysis for insulator pins involves assessing and evaluating various factors. These factors relate to their design, material composition, performance and suitability for the diverse environmental conditions. Additionally, it could involve collaboration with industry experts, utilities and manufacturers. The following are the factors to include in a comparative analysis in south America.
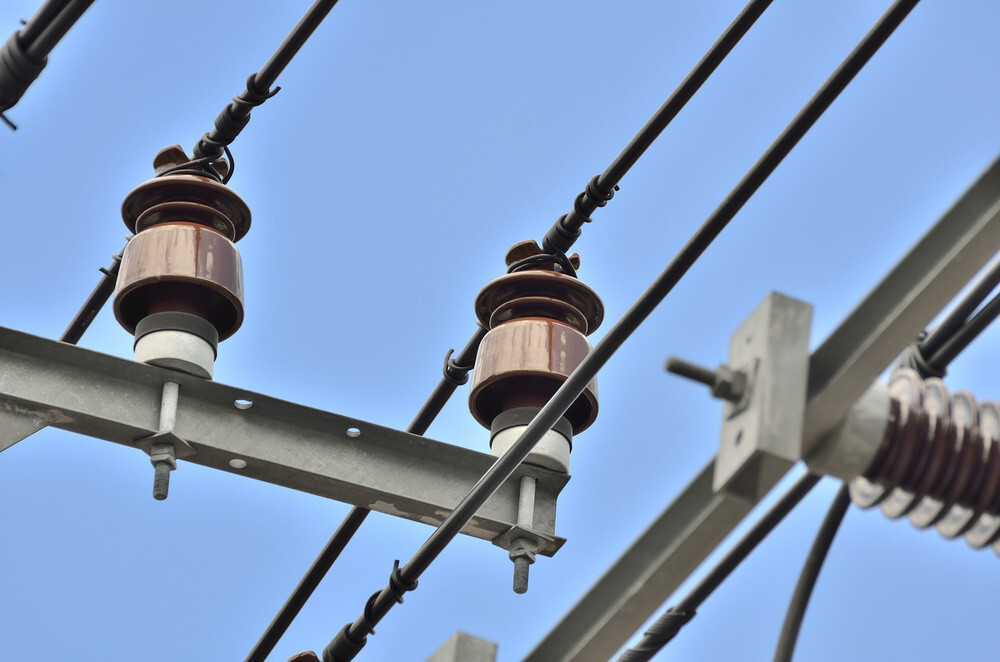
- Material – evaluate the materials used in insulator pins to consider their corrosion resistance. The common materials include steel, aluminum or other alloys.
- Voltage class compatibility – examine the range of voltage classes designed for the insulator pins. Compare the specifications for low-voltage, medium voltage and high-voltage applications.
- Pollution performance – check the pollution performance of insulator pins. Consider their ability to resist contamination and prevent pollution-related flashovers.
- Cost consideration – compare the cost of the insulator pins taking into account the initial costs and long-term maintenance considerations.
- Design – compare the design features of insulator pins. This is including threaded ends, clevis ends or other attachment mechanisms. Check how they impact the installation, stability and compatibility with various insulator types.
- Environmental adaptability – assess how well insulator pins adapt to the diverse environmental conditions.
Certifications and standards in South America
There are various standards and certifications that impact the use of insulator pins in South America. Each south American country has its own set of standards that govern the use of insulator pins. Other countries adopt the various international standards for the insulator pins. Additionally, it is advisable to ensure the selected insulator pin complies with the local standards set. The following are the common types of standards and certifications in South America.
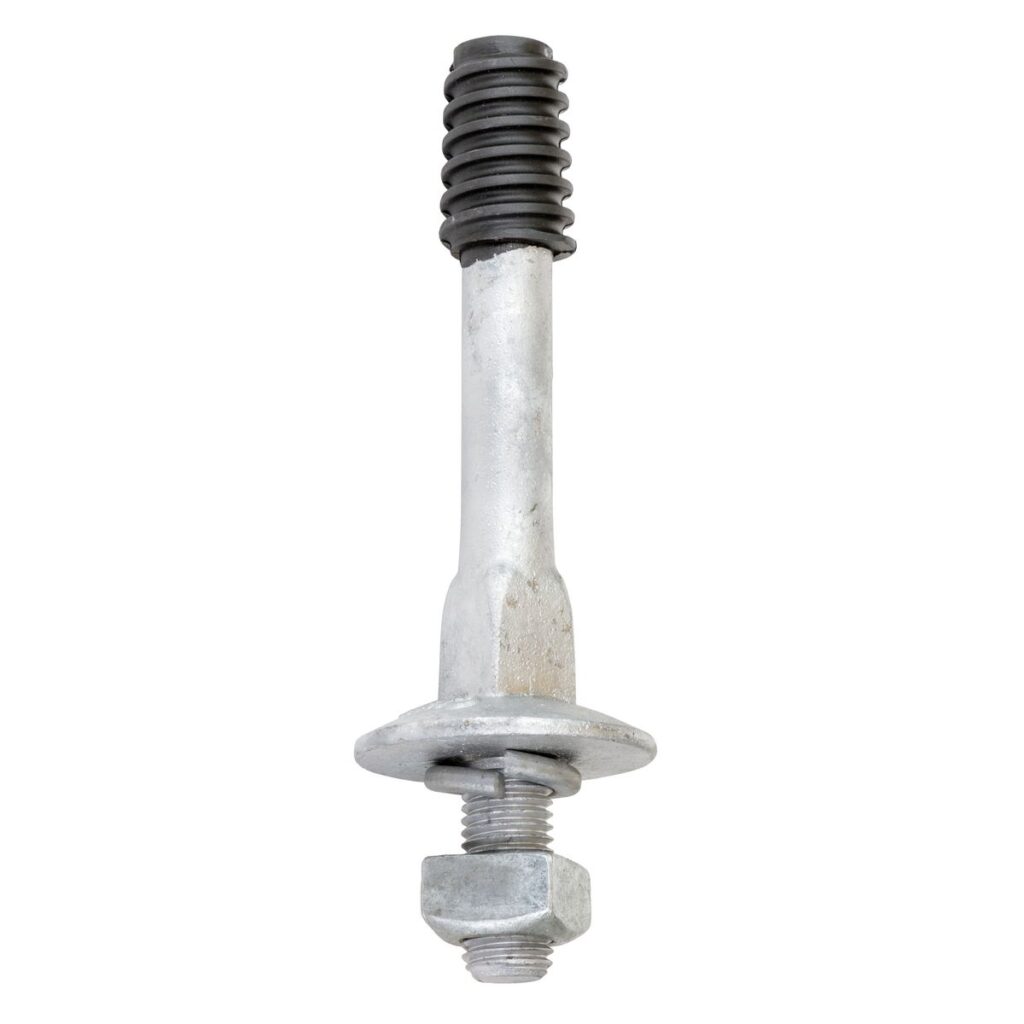
- IEC standards – these are international standards for electrical and electronic technologies. They ensure the compatibility and compliance with global best practices.
- Local national standards – these are the different standards set in different countries for electrical components. Some include the ABNT standards in Brazil and IRAM standards in Argentina.
- ISO certification – this provides international standards for quality management. They also ensure the manufacturers demonstrate compliance with quality assurance standards.
- ANSI standards – these are standards established by the American national standards institute in their regulations.
- Product testing and certification bodies – these are independent testing and certification bodies that validate the performance and safety of insulator pins.
Regional market for insulator pins in South America
There are various factors that promise growth in the South American insulator pin market. These factors include market trends, innovations, manufacturers and suppliers. They also influence the demand and supply of insulator pins in the region. Also, it is advisable to consult industry report, market studies and relevant trade publications. The following are the factors that influence the regional market for insulator pin.
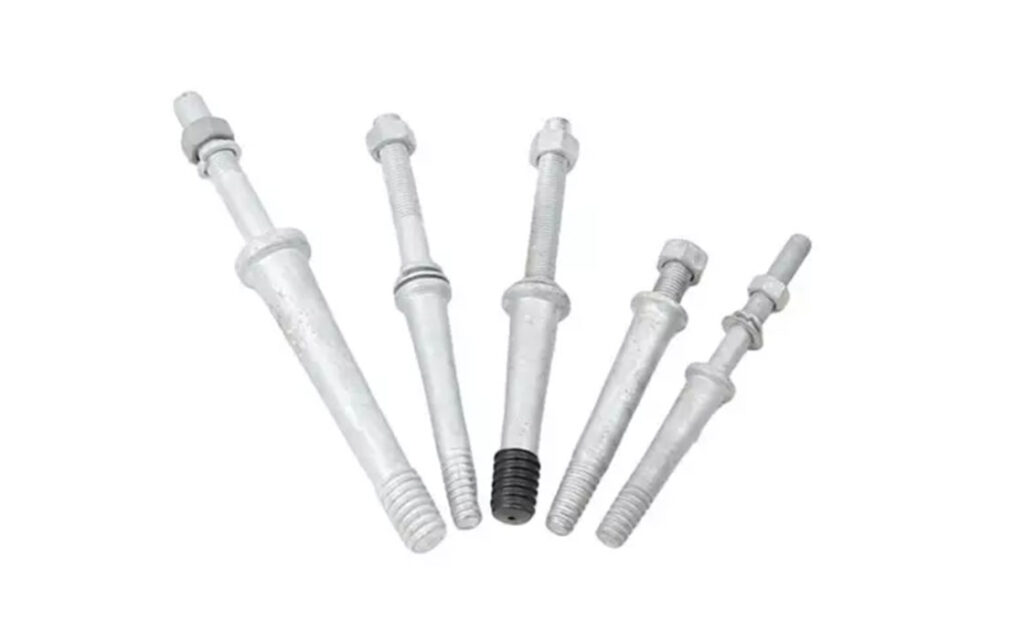
- Increased electricity demand – the increase in population and economic activity leads to the increase in demand for electricity. This also leads to increased demand for transmission networks creating demand for insulator pins.
- Government investment – increased investments in power grids translates to funding for projects that require use of insulator pins.
- Renewable energy success – the continuous embracement of renewable energy sources requires extensive transmission infrastructure. This creates extra opportunities for insulator pin manufacturers.
- Economic trends – this leads to increased funding for energy projects and a higher demand for insulator pins.
- Market competition – increased competition between local manufacturers and suppliers lead to innovation and competitive pricing.
Frequently asked questions
this is a metal component mounted on the crossarm to provide the anchor point to the pin insulator. It acts as a secure base for pin insulators.
An insulator pin is the metal post that mounts on the crossarm of a power pole. It provides the anchor point for the pin insulator to attach to. It functions as a secure base for the pin insulator and helps transmit the weight of the conductor down to the crossarm. A pin insulator is an insulation disc that has a hollowed-out groove on the top side. It provides electrical insulation between the conductor and the pole.