Transmission lines require several types of insulation that ensure the proper transfer of electricity from one point to another. There are various types of insulators used on the lines which are known as electrical insulators. We will discuss one of the insulators known as the pin type insulator or basically, just a pin insulator. A pin type insulator supports and insulates the electrical conductors from the supporting structures. It consists of a porcelain or glass unit mounted on a metal pin. This factor gives it the name “pin type” insulator. The pin type insulator withstands high voltages and provides insulation between the energized conductor and the structure.
Components of the pin type insulator
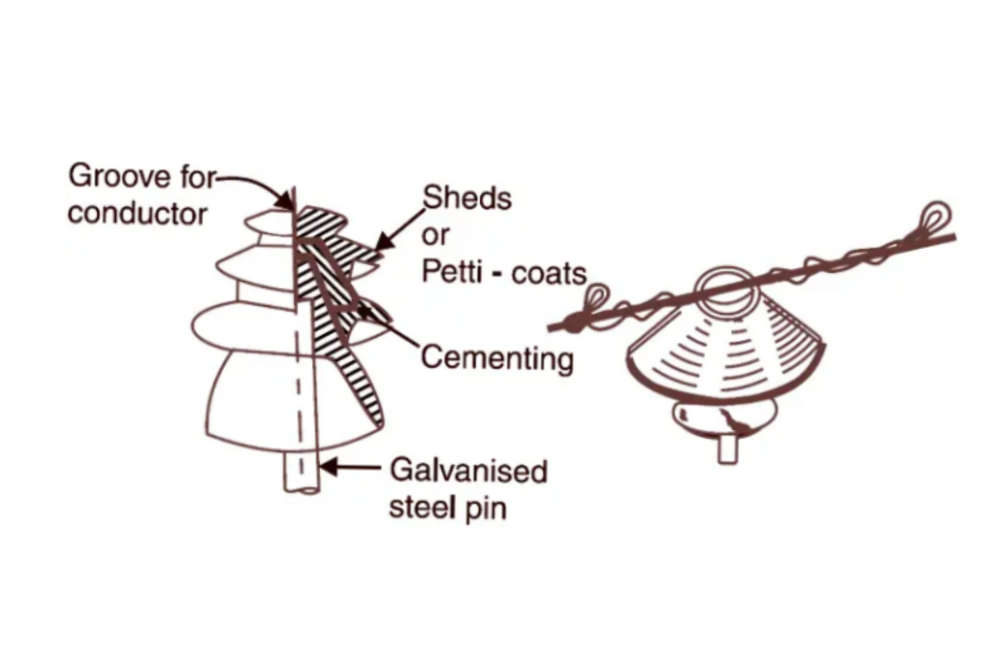
Every device used on the transmission lines has unique features that make energy transfer easier. The components of the pin mounted insulator work together with other fittings to ensure the efficiency and reliability of energy transmission. They also work together to provide electrical insulation, mechanical support, and environmental protection in a pin-type insulator. They also ensure the safe and efficient operation of the overhead transmission lines. Discussed below are the various components of the pin-type insulator.
- Insulating component
The insulting component is the main component of the pin-type insulator made from porcelain and glass materials. These materials help to provide insulation and resist other environmental conditions. The unit is in the form of a cylindrical or disc-shaped structure. - Metal pin
This is a metal rod that serves as the support for the insulating unit made of galvanized steel for corrosion resistance. The metal pin attaches to the supporting structure and provides mechanical strength and stability to the insulator. - Cement
Cement or glaze is used during the installation of the pins to securely attach the insulating unit to the metal pin. It forms a strong bond between the insulator and the pin which ensures the insulating material remains firmly in place even under mechanical stress. - Grooves
The insulating component has grooves on its outer surface which help in distributing the mechanical load evenly and provides additional insulation by increasing the surface distance between the conductor and the supporting structure. - Fittings
Fittings secure the conductor to the pin-type insulator. Such fittings include metal clamps, bolts, nuts and washers among others. They also ensure the reliable connection between the conductor and the insulator maintaining the electrical continuity. - Metal caps
Some of the pin-type insulators have a metal cap on top of the insulating component. This cap provides protection against environmental factors and helps prevent moisture from entering the insulator. - Grading rings
Grading rings are optional components of the pin-type insulator which may be included on the insulating component. They are conductive rings installed near the top of the insulator, designed to distribute the electrical field. They also minimize the concentration of electric stresses and help improve the voltage distribution along the insulator.
Types of pin mounted insulators used on the transmission lines
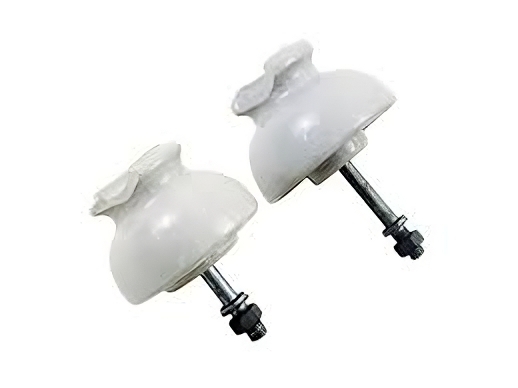
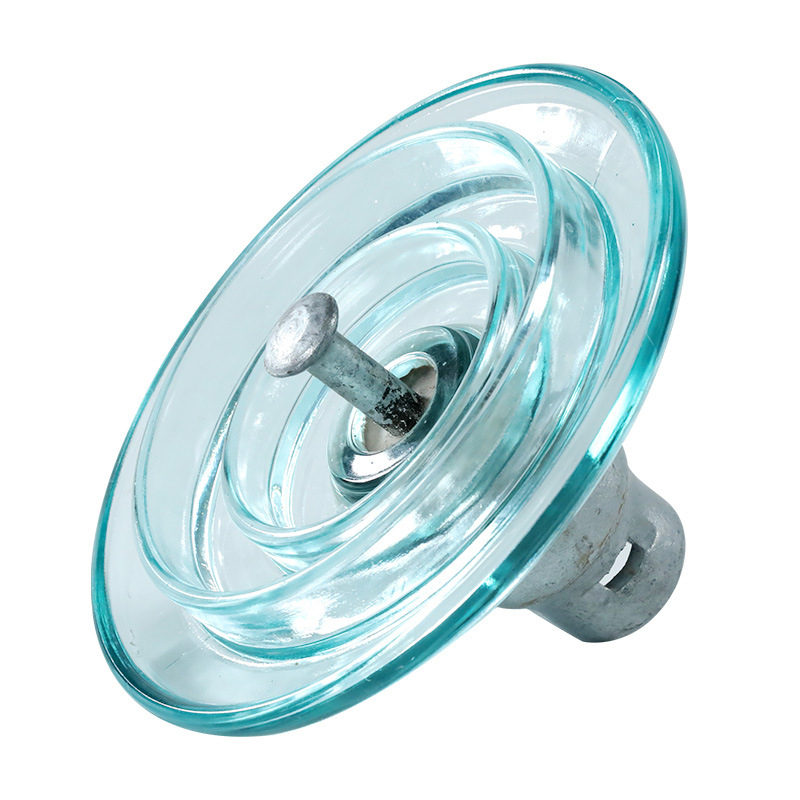
As already discussed, there are various types of insulators used on the transmission for the proper discharge of electrical current. The same applies to the pin type insulators as there are various types used on the overhead lines. Each of the pin type insulators is selected based on the factors such as the voltage level, mechanical requirements, environmental conditions and specific needs of the transmission line system. The common types are discussed below.
- Guy strain insulator – This is used to insulate and support guy wires used to anchor poles or towers. Their design aims to withstand tension and mechanical loads on the overhead transmission lines. They have a disc shape and may be solid-core or multi-piece depending on the voltage requirements.
- Olid-core pin insulator – It is the most common type of pin insulator used for power transmission lines. it consists of a single solid porcelain or glass insulating component mounted on a metal pin. These types of pin insulators work in medium voltage applications and provide good electrical insulation and mechanical strength.
- Composite pin insulator – this kind of insulator is made of a combination of polymer materials like fiberglass reinforced with epoxy. They offer advantages like lighter weight, high strength and excellent resistance to environmental conditions. They must work in areas with high pollution, coastal regions and areas susceptible to the wreckage.
- Multi-piece insulator – In these types of insulators, the insulating component divides into several segments or shells that are stacked together. These insulators offer increased flexibility which allows for easier installation and replacement. They mostly work in low to medium-voltage applications.
- Long-rod insulator – This type of insulator is designed for high-voltage transmission lines which consist of a series of porcelain glass insulator discs connected by metal rods. The long rod design provides increased creepage distance which allows for higher voltage ratings and better performance in polluted environments.
Applications of the pin type insulators
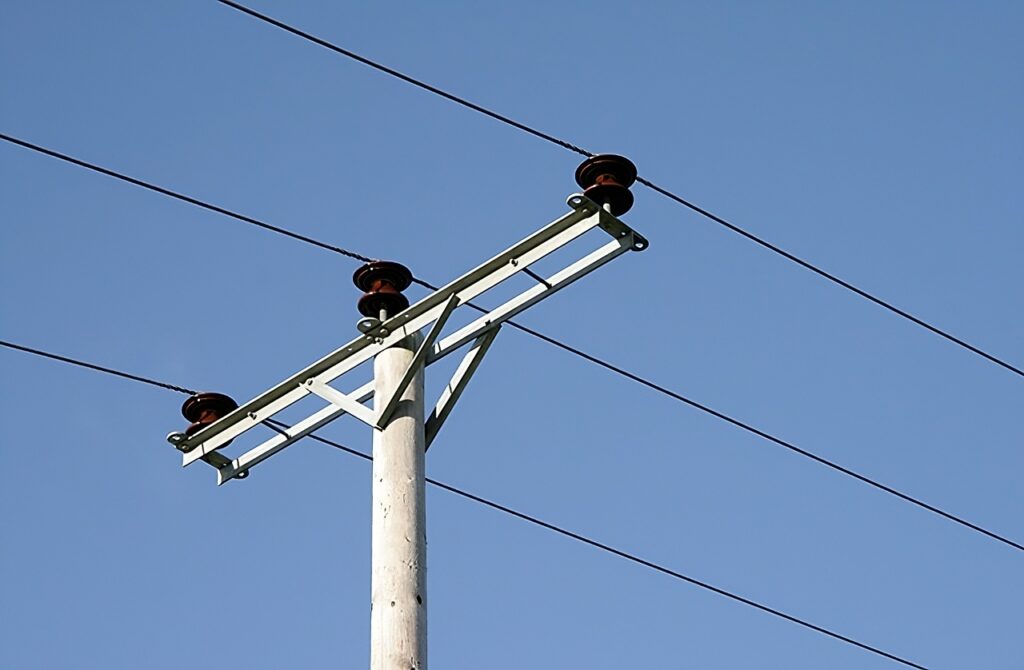
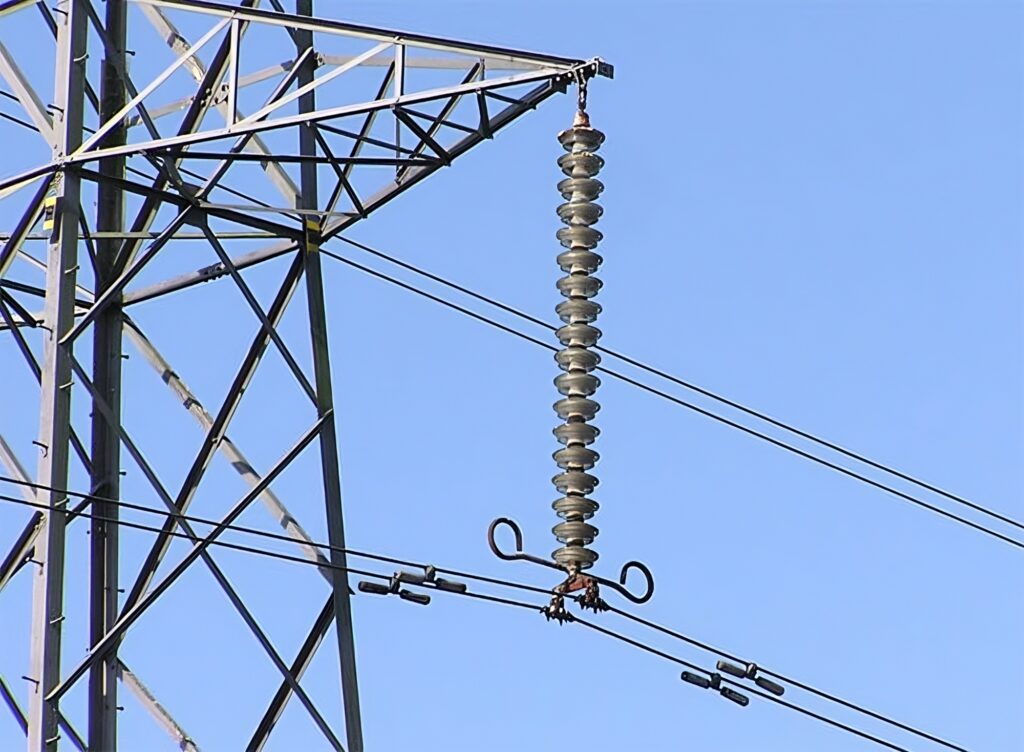
There are many applications in the fields which require the use of pin insulators for proper electricity transmission. The type of pin insulator used in a project depends on voltage level, environmental conditions and the type of power system. The main purpose of the pin type insulator remains to provide electrical insulation, mechanical support and environmental protection in various electrical power applications. The key applications of pin type insulators are as follows:
- Pin type insulators are used to support and insulate the conductors in overhead transmission lines. This ensures safe and reliable transmission of power over long distances.
- The insulators are employed in substations to insulate various equipment and components such as bus bars, disconnect switches and circuit breakers.
- They also work in high-voltage transmission lines with designs and materials that allow them to withstand high electrical stresses and provide adequate insulation for higher voltages.
- Pin type insulators work in distribution lines that carry electricity from substations to residential, commercial and industrial areas. They support the conductor and prevent leakage of current to the supporting structures.
- In electrified railway systems, pin type insulators support and insulate the overhead catenary wires that supply power to the trains. They ensure high-voltage catenary wires are isolated from the supporting structures and the ground.
- They are also utilized in telecommunication lines to support and insulate communication cables. This helps to prevent interference and electrical leakage.
Installation of the pin mounted insulators
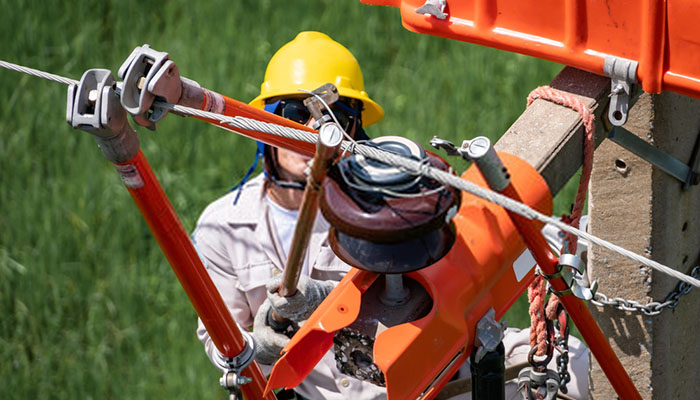
Pin type insulator installation requires careful adherence to safety protocols and industry standards. The specific installation process depends on the system and equipment used. You should also consult manufacturer guidelines and local regulations for specific instructions and requirements. If needed, you should involve experienced professionals or qualified technicians in the installation process to ensure safety and compliance. The following are the steps involved during pin type installation.
- Ensure all the necessary safety measures are in place and verify that the insulators and associated equipment are in good condition and suitable for the voltage end environmental conditions.
- Determine the appropriate locations for installing the pin type insulators along the transmission lines. they are usually placed at regular intervals to support the conductors and maintain proper clearances.
- Attach the metal pin of each insulator to the supporting structure using the appropriate hardware. Ensure that the pins are properly tightened and that the insulators align vertically.
- Connect the conductors to the insulators using suitable fittings such as clamps, bolts or nuts following the manufacturer’s guidelines and industry standards.
- Connect the insulator disc using the provided metal rods in place of long-rod insulators.
- Verify that there is appropriate mechanical clearance between the conductors and other nearby objects. Also, ensure that the conductors are properly tensioned to maintain the desired sag and mechanical stability.
- Conduct a thorough inspection of insulators, fittings and connections to ensure they are secure and free from any defects or damages. Also, perform electrical testing to verify the integrity of the insulation system.
- Establish a regular maintenance and monitoring program to ensure the ongoing performance of the pin type insulators. This involves periodic inspections, cleaning and replacement of any damaged or worn-out components.
How to choose the best pin mounted insulator for your project
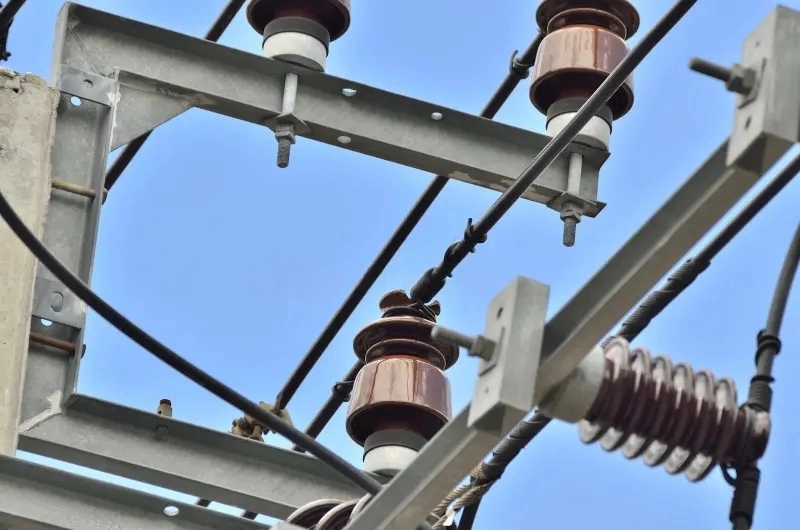
Getting to know whether your application needs a pin insulator and which type to use can be hard sometimes. This is a question often asked by project managers or owners. Pin insulators are vital for power transmission lines that are rated up to 33kV when the voltage goes up and cause the insulators to become inefficient and uneconomical. You could also consult with industry experts or professionals who can provide valuable insights. The following are some factors to consider when selecting a pin type insulator for your project.
- Determine the voltage level of the transmission line since they are available in various voltage ratings.
- Consider the mechanical requirements of the application which include the weight of the conductor, wind loads and tension.
- Evaluate the environmental conditions at the installation site regarding factors like humidity, pollution, temperature variations and seismic activity.
- Consider the material of each pin type insulator and which works with your kind of application.
- Choose an insulator with good pollution performance which can resist the accumulation of contaminants which reduces the risk of flashovers and maintains the insulation performance.
- Evaluate the electrical characteristic of the insulator to determine the insulator’s ability to withstand electrical stresses and maintain effective insulation.
- Consider the relevant international or local standards and regulations governing the selection and use of pin type insulators.
- Consider the reputation and reliability of the manufacturer or supplier who should have a track record of delivering high-quality insulators and providing excellent customer support.
FAQs
Electrical insulation
Mechanical support
Environmental protection
Easy installation and maintenance
An insulator pin is also known as a line post insulator used to mount insulators on supporting structures. It is cylindrical in shape and provides a stable base for the insulator. A pin type insulator is used in overhead transmission lines to support and insulate electrical conductors. It is designed to provide electrical insulation.
Voltage limitations
Mechanical stress
Require maintenance
They are fragile
Relatively heavy
High costs