A side tie is a component used in overhead and electrical installations to secure the conductors. It secures the conductors to the insulators to ensure electrical stability and safety. It consists of a piece of wire that wraps around both the conductor and the insulator to hold them in place. The main purpose of the side tie is to prevent the conductor from moving or detaching from the insulator. Side ties consists of durable materials such as aluminum, copper or similar conductive metal. A side tie works with an insulator to separate the conductor from the utility poles to prevent unwanted current flow. Side ties also reduce conductor vibrations caused by wind and other environmental factors. They work in overhead transmission lines, telecommunications and industrial applications.
Functions of a side tie
A side tie serves various functions that ensure the stability, safety and reliability of power distribution systems. Their roles help in ensuring the long-term stability and safety of overhead transmission lines. The following are the common functions of side ties in various applications.
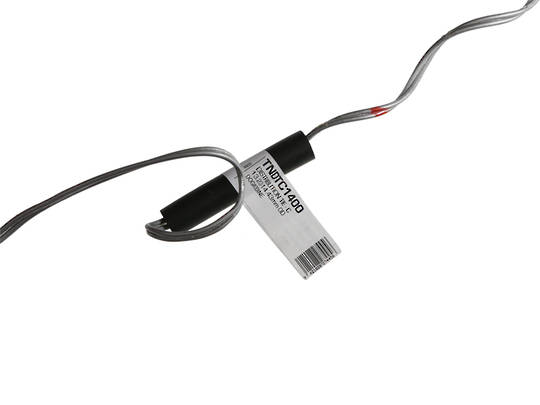
- Securing conductor to insulators – the side tie attaches the conductor to the insulator. This is to prevent the conductor from becoming loose or detached.
- Maintaining electrical continuity – the tie maintains electrical continuity along the power line. This is to ensure there are no interruptions in the electrical path to deliver reliable power to consumers.
- Reduction of conductor vibrations – conductor vibration and swinging can lead to wear and damage. Side ties help to dampen these vibrations to reduce swinging and extend their lifespan.
- Handling mechanical loads – side ties distribute these loads across the insulator and reduces the risk of damage.
- Thermal expansion and contraction – conductors expand and contract with temperature changes. This can lead to conductor sag. Using side ties allows for some movement of the conductor to accommodate the thermal expansions and contractions.
- Insulation support – side ties aid maintaining the electrical insulation of the systems. They also ensure the conductor remains positioned on the insulator to prevent electrical arcing.
- Enhancing safety and reliability – the ties also enhance the safety and reliability of the power systems. This is by ensuring the power supply remains stable and consistent.
- Ease of maintenance and inspection – side ties are easy to install, inspect and maintain. This makes it simple for utility workers to check the integrity of the attachment.
Technical specifications for a side tie
The technical specifications for side ties are important to ensure the stability, safety and reliability of the system. Additionally, the manufacturers should provide technical specifications for the side ties during purchase. The following are the key technical specifications for side ties.
Catalog Number | Diameter Range Min | Diameter Range Max | Applied Length (inches) | Insulator Identification Mark | Color Code |
CST-24 | .278 | .315 | 24 | Black/None | Purple |
CST-25 | .406 | .459 | 25 | Black/None | Blue |
CST-27 | .460 | .520 | 27 | Black/None | Orange |
CST-28 | .521 | .588 | 28 | Black/None | Red |
CST-31 | .589 | .665 | 31 | Black/None | Purple |
CST-33 | .666 | .755 | 33 | Black/None | Brown |
CST-35 | .756 | .858 | 35 | Black/None | Red |
CST-36 | .859 | .968 | 36 | Black/None | Blue |
CST-38 | .969 | 1.096 | 38 | Black/None | Green |
- Material specifications – side ties are from materials like aluminum, aluminum alloy, galvanized steel or copper. These materials ensure good electrical conductivity, corrosion resistance and durability. The materials selected should be compatible with the conductor to avoid galvanic corrosion.
- Design standards – these standards include dimensional accuracy and conductor size compatibility. The design must have the precise dimensions to ensure a proper fit around the conductor and insulator.
- Mechanical properties – the side tie must have enough tensile strength to withstand the mechanical loads imposed by the conductor. The material should also have enough elasticity to accommodate movements of the conductor. The side tie should also dampen vibrations to prevent fatigue damage to the conductor.
- Electrical properties – the material should have high electrical conductivity. This aids in reducing potential heating effects. It must have designs to work with insulators that prevent unwanted current flow.
- Load ratings – side ties must support the static load of the conductor including its weight and extra loads. It should also withstand dynamic loads due to wind and other factors.
- Installation specifications – the specifications should include guidelines for tools and techniques required.
Cost comparisons and considerations for side ties
Costs for side ties can vary depending on materials, design, and installation needs. It is also important to consider the long term costs including maintenance, replacement and compliance. Additionally, selecting the right side tie needs balancing upfront expenses with total cost of ownership. This is to ensure the most cost effective and reliable solutions of your specific application. The initial cost per unit ranges between $3 to $10 depending on various factors. The following are the factors to consider when checking the costs for side ties.
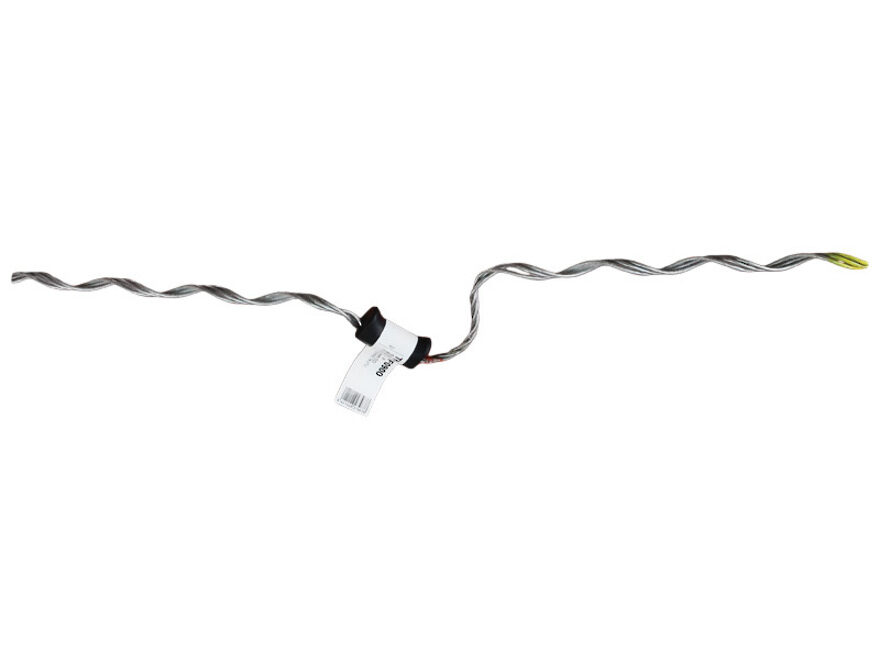
- Materials costs – aluminum is light weight and corrosion resistant. The price ranges from $1 to $3 per unit depending on the quality and size. Galvanized steel provides durability and strength making it more expensive than aluminum. Prices ranges between $2 to $5 per unit. Copper is more expensive ranging between $4 to $8 per unit. Composite materials are costly ranging from $5 to $10 per unit.
- Design costs – preformed ties are more expensive due to costs related to precision shaping and fitting. Prices ranges between $2 to $6 per unit. Hand-tied options are less expensive costing $1 to $3 per unit but need more labor.
- Installation costs – installation costs vary depending on the complexity of the installation and the location. Preformed ties reduce installation time leading to lower labor costs. Side ties that need specialized tools for installation adds to the cost.
- Environmental considerations – higher-cost materials like galvanized steel or synthetic materials are necessary in areas prone to high corrosion. Ties that need to withstand extreme weather conditions need extra treatments or coatings which increases their cost.
- Maintenance costs – using durable materials like galvanized steel and high quality aluminum can reduce maintenance costs. The ease of inspection and replacement of the side ties can affect the costs.
Supplier information for side ties
Selecting the right supplier for side ties helps to ensure quality, reliability and cost effectiveness. The right supplier should meet both the current and future needs of the applications. This contributes to the success and sustainability of the project. TTF Power Technology provides a wide range of power line hardware. We offer products like power line hardware, pole line fittings, conductor hardware and insulators. Additionally, it is advisable to ask for quotations from different suppliers before selection. The following are the factors to consider when selecting the supplier for side ties.
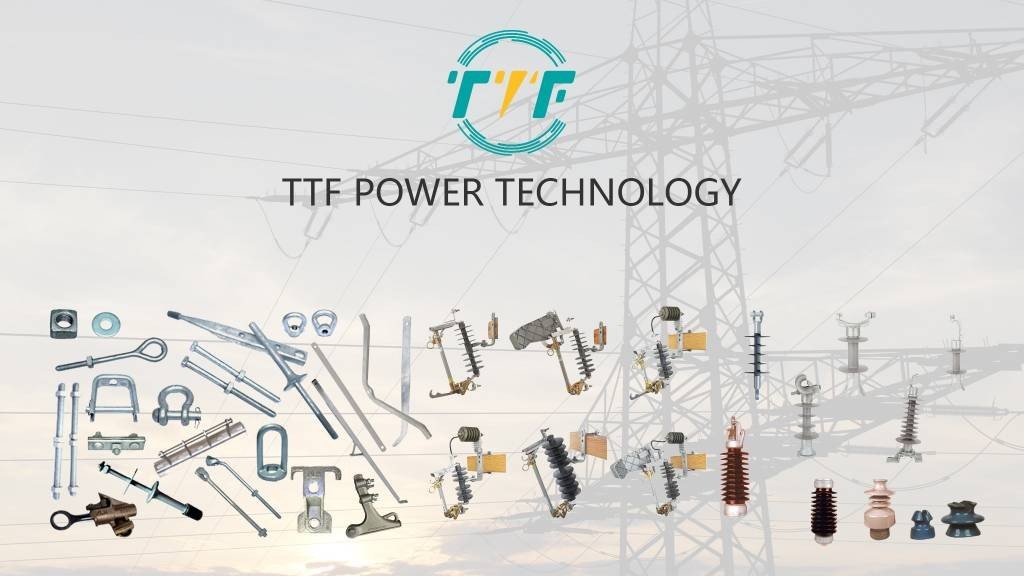
- Quality assurance – ensures the supplier’s side ties meet relevant standards like ANSI, IEEE, IEC and regional standards. Check for certifications such as ISO 9001 for quality management systems.
- Material quality – verify that the materials used for the side ties match the project’s requirements.
- Supplier reputation – select suppliers with a proven track record in manufacturing side ties for electrical installations. Check previous customer’s reviews to gauge the supplier’s reliability and reputation.
- Cost considerations – compare the cost per unit from different suppliers and balance quality with the costs. Check for suppliers who provide discounts for large orders to reduce the costs for various projects. Consider the total cost of ownership including maintenance, replacement and potential downtime.
- Delivery and lead times – check the supplier’s inventory levels to ensure they meet your project’s timeline. Check the lead times for manufacturing and delivery of the suppliers. This is to ensure they provide reliable logistics networks.
- Supplier innovation and technology – select suppliers who invest in research and development. This ensures that they provide the latest innovations in side tie technology. Check their use of modern technology in manufacturing processes. This helps to ensure consistent quality and efficiency.
Community forums and interactions for side ties
Engaging with community forums and industry groups can be valuable when dealing with side ties for installations. These platforms provide opportunities for networking, knowledge sharing and staying updated with the latest technologies. Also, they allow you to connect with industry experts and enhance your project outcomes. The following are the platforms and groups related to side ties.
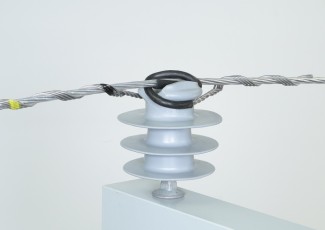
- Online community forums and communities – this may include Electric Power Research Institute Forum. They provide platforms for professionals to discuss technical issues, share research and explore advancements in electric power.
- Industry-specific platforms – these include Power & Energy Society, National Association of Electrical Distributors and Power and Energy Society of Great Britain. They provide forums and resources for professionals to discuss technical and industry-related topics.
- LinkedIn groups – join industry-specific groups such as Electric Power Professionals or Transmission & Distribution. They help in networking with professionals, sharing articles and participating in discussions about side ties.
- Reddit – subreddits allow you to ask questions, share experiences, and discuss innovations related to electrical installations.
- Facebook groups – join Facebook groups that share practical experiences and provide guidance from a community of electrical professionals.
Frequently asked questions
Side ties help in maintaining the integrity and safety of overhead transmission systems. They prevent conductor movement, reduce wear on the insulators and reduce mechanical failure.
Key specifications include material type, tensile strength, corrosion resistance and thermal properties. It also includes compatibility with insulator and conductor types.
These factors include initial purchase price, installation costs, environmental durability and compliance with regulations.