A big grip dead end is a type of hardware used to terminate or anchor overhead conductors on transmission lines. It has a design that provides a secure attachment point and prevents the conductors from coming loose or sagging excessively. “Big grip” refers to the type of gripping mechanisms used in dead-end hardware. It consists of a set of serrated jaws that grip the conductor tightly and provides a strong and reliable connection. The “dead end” is the point at which the conductor terminates or ends. It is the last point along the transmission line before the conductor is anchored or terminated. The purpose is to ensure the stability and integrity of the conductor in overhead transmission lines and maintain proper tension while minimizing the risk of sagging or detachment.
Parts of the big grip dead end
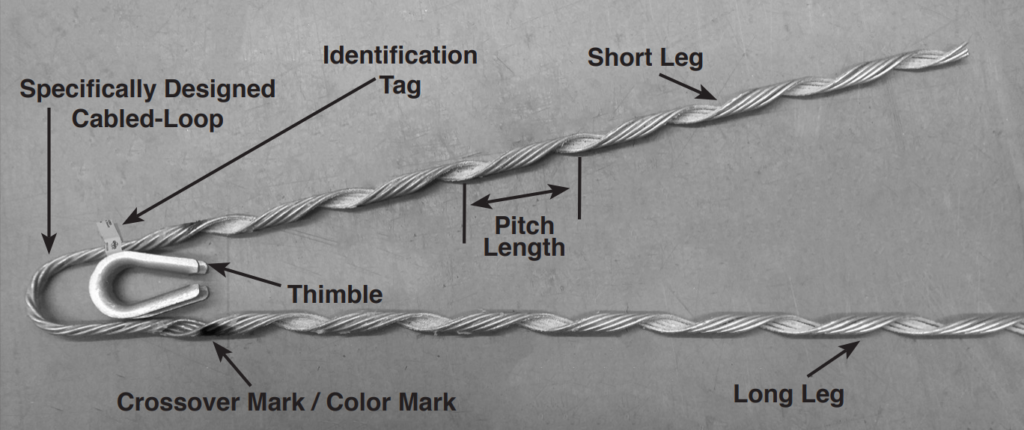
The components of the devices vary depending on conductor type, voltage rating and manufacturer’s specifications. Below are the common components of the big grip dead end.
- Grips
These are the main components responsible for gripping the conductor which consists of serrated jaws or clamps made of high-strength materials such as steel. - Preformed rods
Preformed rods are typically made of high-strength materials like aluminum steel which provide structural support to the grip. This helps maintain the desired shape and alignment of the dead-end assembly. - Dead end sleeves
These are protective sleeves made of insulating materials like rubber or composite polymers. They mainly cover and insulate the gripping area where the conductor is in contact with the grip. - Thimble
Thimbles are protective metal fittings placed inside the grip to protect the conductor from abrasion or damage. - Structural components
Structural components include bolts, nuts, washers and other fastening hardware. They secure the components together and provide structural integrity. - Anchoring hardware
Additional anchoring hardware may be included to secure the dead-end assembly to the supporting structure.
Types of big grip dead ends
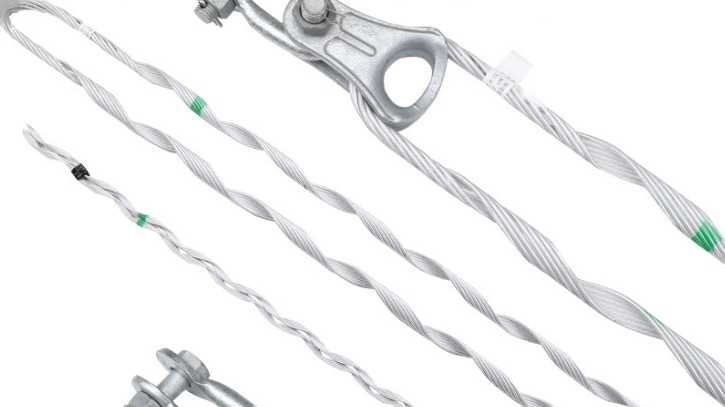
The types of the big grip dead end vary depending on the specific requirements of the transmission lines. Others also depend on the manufacturer and suppliers in the market. The following are the main types of line dead end.
- Swage dead end
They use mechanical swaging techniques to create a permanent connection between the grip and the conductor. Swaging involves compressing the metal around the conductor creating a secure and low resistance joint. - Bolted dead end
Bolted dead end uses bolts and nuts to secure the grip to the conductor which offers a strong reliable connection and is commonly used for medium to high voltage overhead transmission lines. - Armor rod dead end
This type incorporates additional components known as armor rods which provide additional protection and support. This reduces the risk of abrasion and damage. They are mostly used in areas prone to high wind or vibration. - Compression dead end
The compression type utilizes compression fittings to secure the grip onto the conductor. They are designed to create a tight and durable connection without the need for bolts or other tools. - Hydraulic dead end
Hydraulic type uses hydraulic pressing methods to achieve a reliable and robust connection. They are designed for high-tension applications and handle significant loads.
Application of the dead end
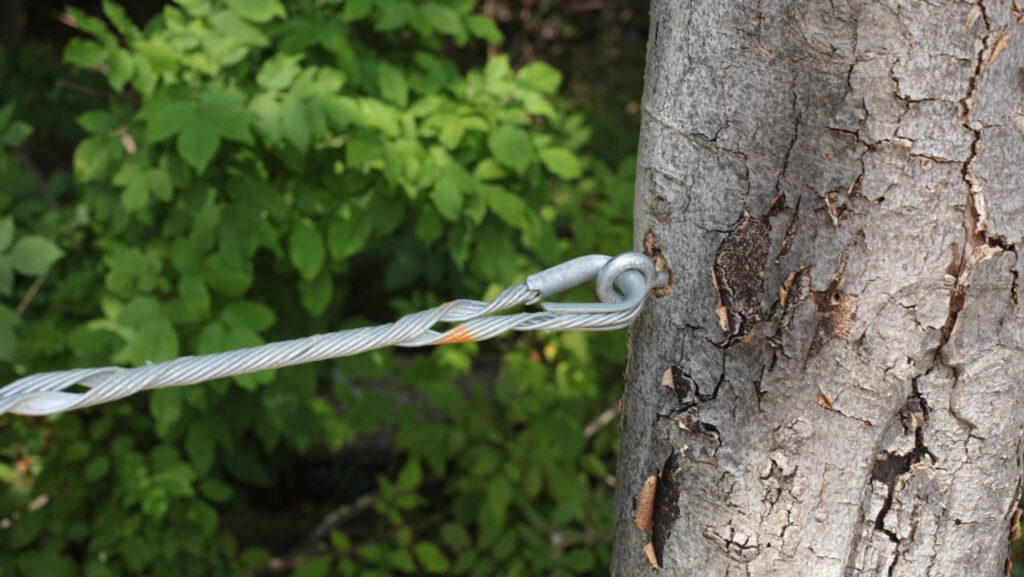
The application of this product depends on the design of the transmission lines, conductor type, voltage rating and other factors. They are used on various applications to ensure termination and proper tensioning of conductors. The following are the application of the big grip dead end.
- Line angle changes – This is in areas where transmission lines change direction or angle to accommodate the variation.
- Dead-end terminations – These apply at the ends of transmission lines to terminate conductors securely. This provides reliable attachments point to prevent the conductor from being loose.
- Temporary connections – This type is used for temporary connections during construction or maintenance activities.
- Tensioning – they play a crucial role in maintaining proper tension in overhead transmission lines. This is by securely gripping the conductor and distributing the applied load evenly which helps prevent excessive sagging or stretching.
- Guyed structure – big grip dead ends are employed in guyed structures where additional support is provided to the transmission line using guy wires or cables.
Installation of line dead ends
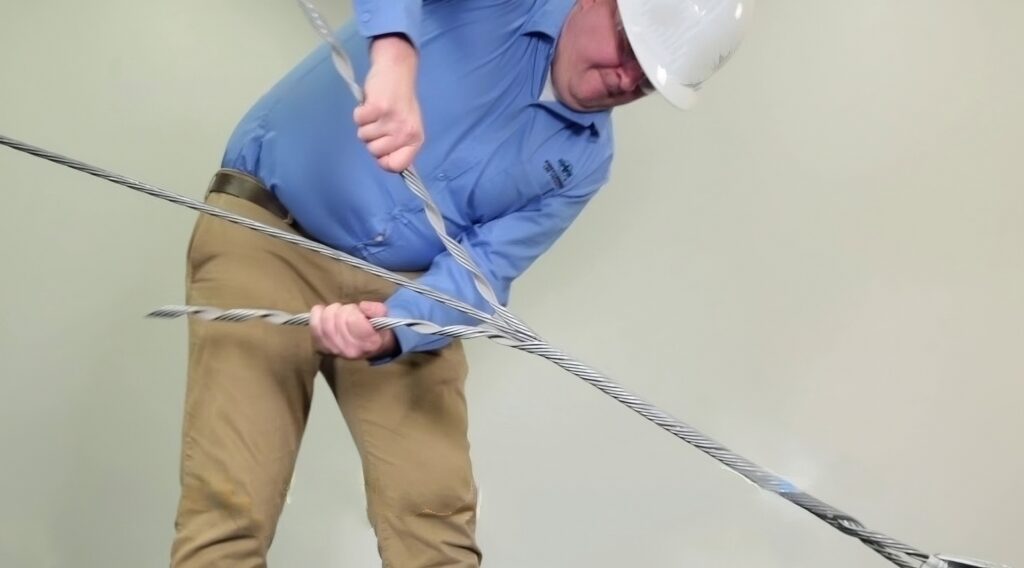
The installation process depends on the instructions provided by the manufacturer of the devices. It is advisable to consult with a qualified professional for the installation process if in doubt. The following is a basic series of steps used for the installation process.
- Ensure that you have the appropriate tools and equipment for the job which includes wrenches, torque wrenches, hoists, insulation removal tools and safety equipment before the installation.
- Inspect the conductor and the area where the big grip dead end will be installed. Check for signs of damage, corrosion or wear that may affect the installation or performance.
- Clean the conductor surface where the big grip dead end will be attached. Remove any dirt, grease or corrosion using an appropriate cleaning agent.
- Follow the manufacturer’s instructions to assemble the components of the big grip dead end. This involves using attaching the grip, thimbles and other fittings as required.
- Attach the big grip dead end over the stripped conductor end. Make sure the conductor is fully inserted into the grip and properly aligned. Use the appropriate fasteners like bolts, nuts and washers to secure the connections.
- Install any insulation if required and ensure they cover the gripping area for proper protection.
- Perform any required tests or tensioning procedures as specified by the manufacturer or engineering standards.
- Keep a record of the installation which can be useful for future maintenance and inspections.
Choosing the best dead end for your applications
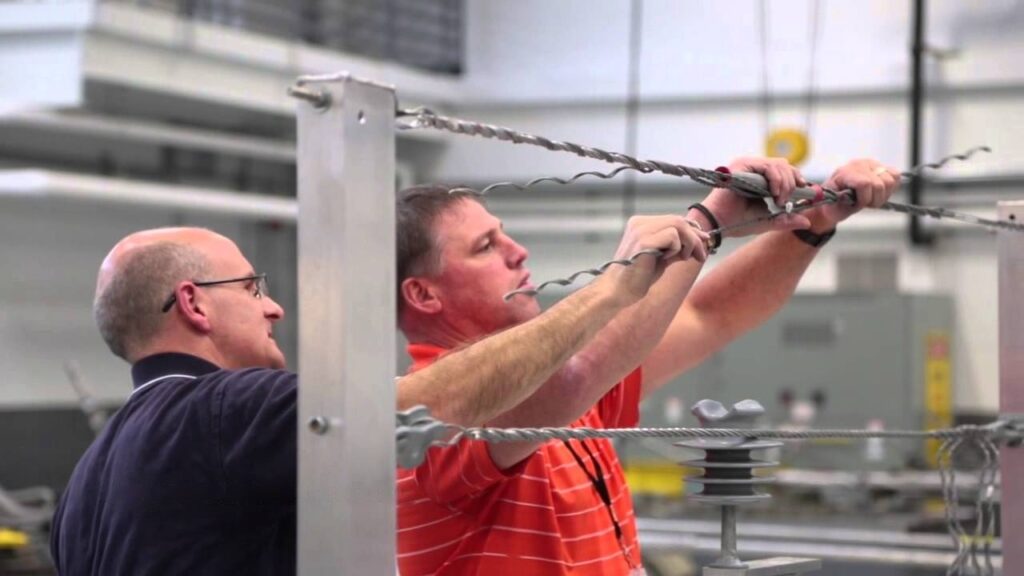
You can select the best big grip dead end that meets your specific needs which ensures a reliable and secure termination of your transmission line conductors. The following are the factors to consider before selecting the device for purchase.
- Consider the type and size of the conductor you will be working with. Big grip dead ends are designed for specific conductor materials and different size ranges.
- Determine the voltage rating of your transmission line and make sure the kind of dead end meets the voltage requirements of your application.
- Evaluate the load capacity or tensile strength of this line dead end and consider the maximum tension the dead end can handle without compromising performance or safety.
- Consider the environmental conditions where it will be installed.
- Select dead ends from a reputable manufacturer known for producing high-quality products.
- Consider any specific requirements or challenges of your application considering factors like line configuration, anticipated loads or other specifications depending on your application.
- Seek guidance from transmission line engineers, consultants or industry professionals who have experience with this product.
FAQs
It is a type of hardware used to terminate and anchor overhead conductors on transmission lines. It provides a secure attachment point and helps maintain proper tension in the conductors.
Regular inspection and maintenance are essential to ensure the ongoing performance and safety of this line dead end.
Ease of installation
Durability
Tension maintenance
Secure termination
Temporary connection capability
Industry compliance
Compatibility
Limited application range
Installation complexity
Maintenance and complexity
Reusability challenges
Safety considerations