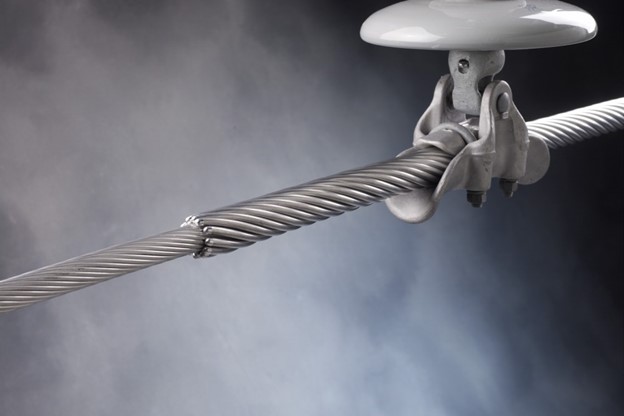
An armor rod is a device used to provide mechanical protection to the conductor. It also enhances the grip between the conductor and suspension clamps. Armor rod is also known as a rod armor or cable armor rod. It is from a helically wound structure that wraps around the conductor. They are from materials such as aluminum or galvanized steel. These materials help them resist rust and corrosion and increase durability. Armor rods often position between the suspension clamp and the conductor to ensure a reliable and secure connection. Common types include single-helix, double-helix, cross-armor, thimble ended and helical armor rod. They find use in applications such as transmission lines, tension clamps and corner installations.
Benefits and applications of armor rod
Armor rods offer various benefits that protect the cables from various external factors. These benefits include abrasion resistance, improved performance, reduced maintenance costs, enhanced system reliability and simple installation. The armor rods find use in various applications as discussed below.
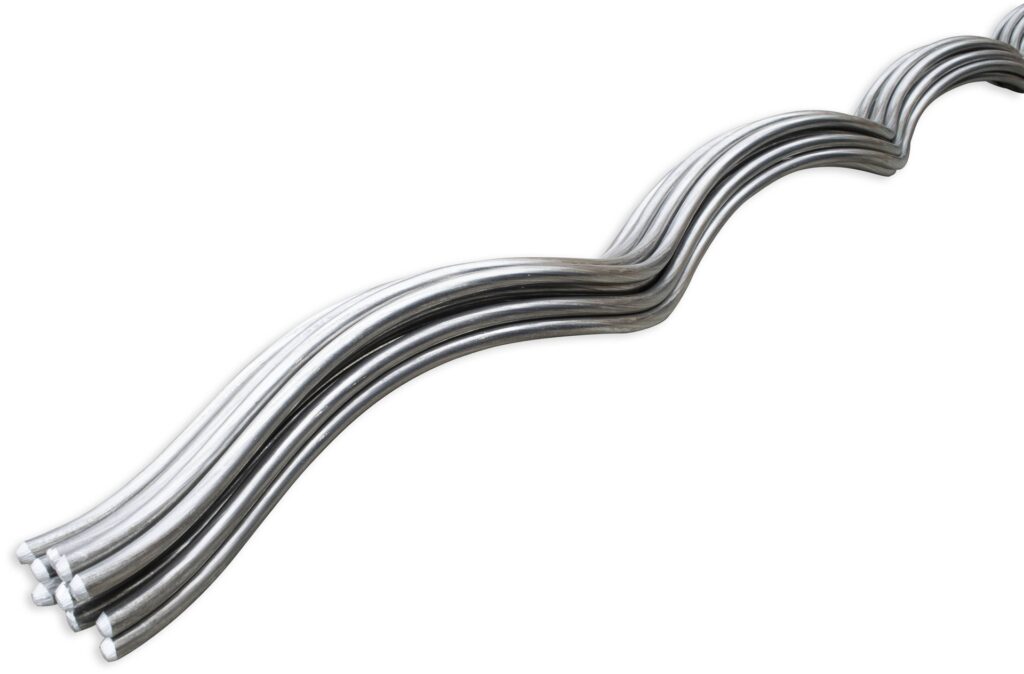
- Anti-vibrations – the armor rods help reduce the vibrations from wind, cable movement or other factors. This helps provide stability and performance of the cable and reduce the risk of fatigue.
- Cable protection – the rods provide mechanical protection to the cable. They act as a shield and wrap around the cable. They also prevent damage to the cables outer jacket and maintain its integrity.
- Compatibility – they are compatible with various cable types like transmission lines, OPGW and ADSS cables.
- Grip enhancement – they also improve the grip between the cable and other components. The grip ensures secure connections and reduces the risk of slippage.
- Load distribution – armor rods distribute mechanical loads along the length of the cable. They cut stress concentration points and reduce the risk of damage or failure.
- Corrosion resistance – they are from aluminum alloy which provides protection against corrosion. This makes them suitable for outdoor applications with presence of moisture and humidity.
Challenges and issues associated with armor rod
As mentioned earlier, armor rods offer various benefits to support the conductors and overhead cables. However, they also come with various limitations and challenges. It is thus advisable to weigh the benefits and challenges of using armor rods against the specific needs. The following are the various challenges associated with use of armor rods.
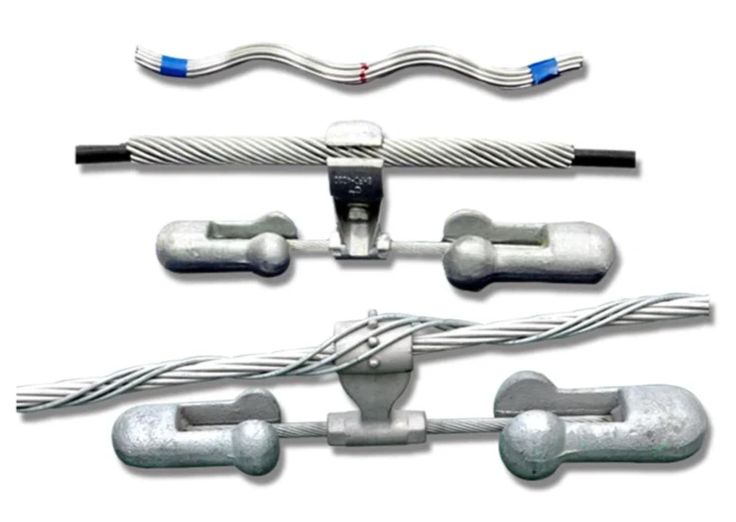
- Material – armor rods are from various materials that contribute to their effectiveness. These materials include aluminum, steel and galvanized steel. Aluminum can be susceptible to corrosion which can compromise their strength. Galvanized steel prevent corrosion but they come at high costs.
- Flexibility – integration of armor rods increases the weight of the cable. The weight which may limit applications requiring high flexibility. They may also limit the cables bending radius which hinders flexibility.
- Installation and maintenance – installation of the armor rods needs skills and expertise. This is to ensure proper tension and coverage. They need frequent inspection to identify the potential damage to the equipment.
- Costs – the initial costs for buying and installation are significant for large projects. Use of armor rods might be an unnecessary expense if used where cables face minimal risk of damage.
- Compatibility – the armor rods should be compatible with existing cable insulation. This is to avoid potential chemical reactions.
Selection criteria for armor rod
The selection for armor rods should ensure they are compatible with the specific line configuration, conductor type and environmental conditions. proper selection also ensures ideal cable protection and system performance. Additionally, it is advisable to consult industry experts for guidance. The following are the factors to consider when selecting armor rods.
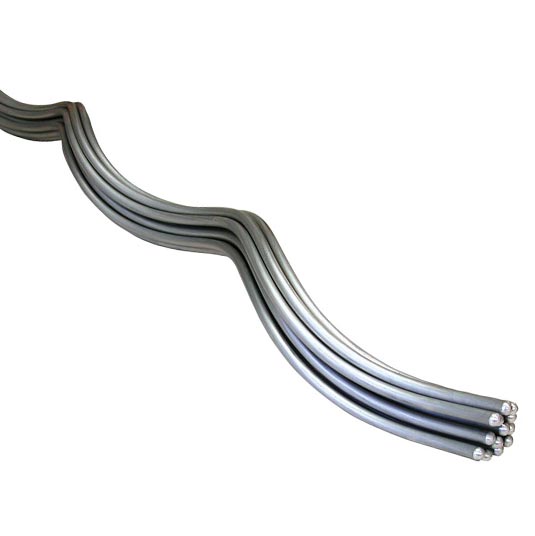
- Armor rod properties – consider the material used in the manufacture of the armor rods. Galvanized steel offer superior corrosion resistance and may come at a higher cost. Select a rod thickness that provides protection against stress and damage. Examine the finish to ensure minimal abrasion risks.
- Costs – compare the initial costs and installation against the potential saving from extended cable lifespan. Analyze the level of risk the cable handles in the environment and establish proper protection methods.
- Compatibility – ensure the selected armor rod material is compatible with the existing cable insulation.
- Sustainability – select armor rods that are from environmentally friendly materials to reduce their ecological impact.
- Installation method – choose an armor rod type suitable for your preferred installation method. Factor in the labor costs and complexity for large projects.
- Aesthetics – consider the visual impact of the armor rod materials and finish. This helps to ensure the discreet appearance.
- Cable diameter and type – select armor rod size that matches the cable diameter for proper fit and coverage.
- Environmental conditions – examine the environmental conditions the cable will handle. This is including moisture, salt exposure, extreme temperatures or direct sunlight. Select materials that offer corrosion resistance.
Installation of armor rods
The installation process of the armor rods should ensure the longevity, reliability and effective performance of the transmission system. Additionally, follow the manufacturer instructions and industry best practices for successful installations. The following is a basic process of the installation.
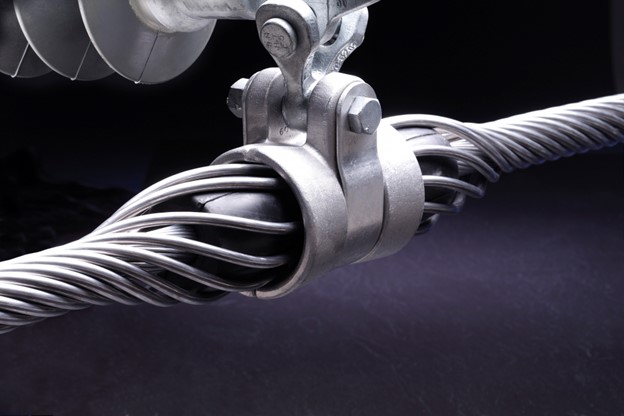
- Ensure you have all the necessary tools and equipment on hand. This is including safety gear, wrenches, cable lubricant and specialized tool recommended.
- Clean the conductor’s surface where the armor rods will install. This is to ensure a clean and secure connection between the conductor and the armor rods.
- Apply the suitable lubricant if recommended to help ease the installation process. It also prevents damage to the conductor.
- Choose the installation points near the suspension or tension clamps.
- Place the armor rods over the conductor at the selected installation points. Ensure they orient and wrap around the conductor.
- Wrap the armor rods around the conductors by hand to maintain the alignment of the armor rods and ensure they fit.
- Secure the ends using the provided locking mechanisms, clips or fasteners.
- Maintain the recommended spacing between the armor rods as specified by the manufacturer. This is to ensure proper coverage along the length of the conductor.
- Inspect each armor rods to ensure they are properly secured and aligned.
Maintenance and safety tips for armor rods
Maintenance of armor rods ensure the performance and reliability of overhead transmission lines. The checks help identify wear, damage or other issues that might affect the grip and protection provided by the rods. Regular maintenance ensures the armor rods continue to provide effective protection. Maintenance of the armor rods is as discussed below.
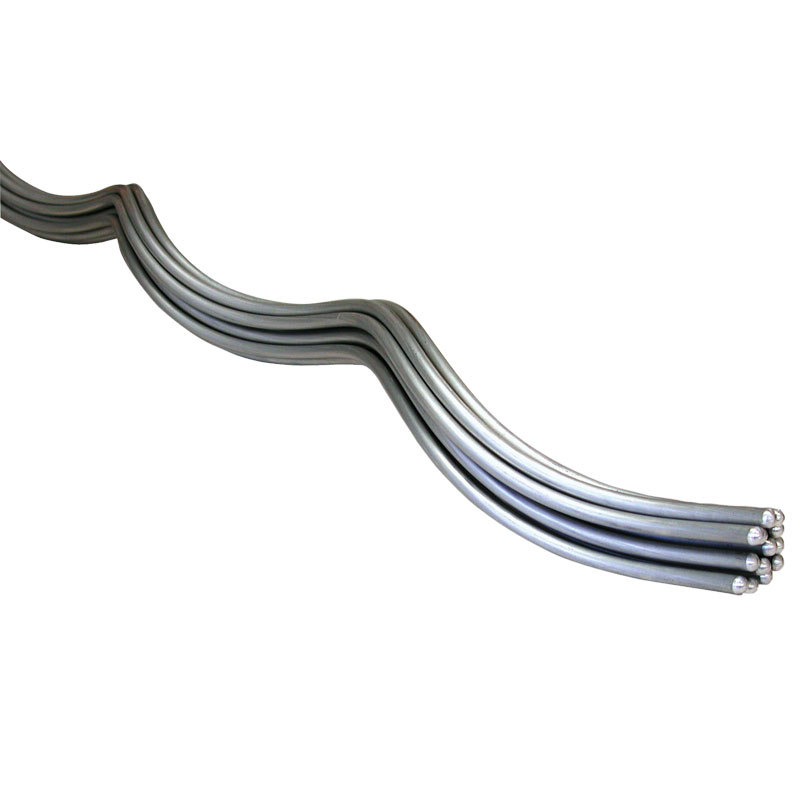
- Conduct regular visual inspections of the armor rods and look for signs of wear, damage or cracks.
- Ensure the armor rods are properly aligned and positioned in the conductor. Look for any misalignment, movement or sliding.
- Check that the spacing between the armor rod is consistent and within the manufacturer’s recommendations.
- Verify that the ends of the armor rods are securely attached and fastened according to the guidelines.
- Look for signs of corrosion or rust in the armor rods to prevent weakening of the material.
- Clean the armor rods to remove dirt, debris and contaminants which helps to prevent abrasion and maintain the grip.
- Apply lubrication to the conductor surface before installing the armor rods if applicable. This helps to ease the installation process and reduce friction.
- Replace any armor rod that shows signs of wear, damage or corrosion to ensure reliability.
- Establish a regular maintenance schedule for inspecting and maintaining armor rods
- Document records of maintenance activities and any replacements performed. This is to help keep track the condition of the armor rods over time.
Cost considerations for armor rods
The cost of the armor rods varies depending on various factors that help to select suitable and affordable rods. Balance the initial costs with performance, maintenance costs and reliability. Proce for armor rods also depend on the selected manufacturer or supplier. The following are the factors that influence pricing for armor rods.
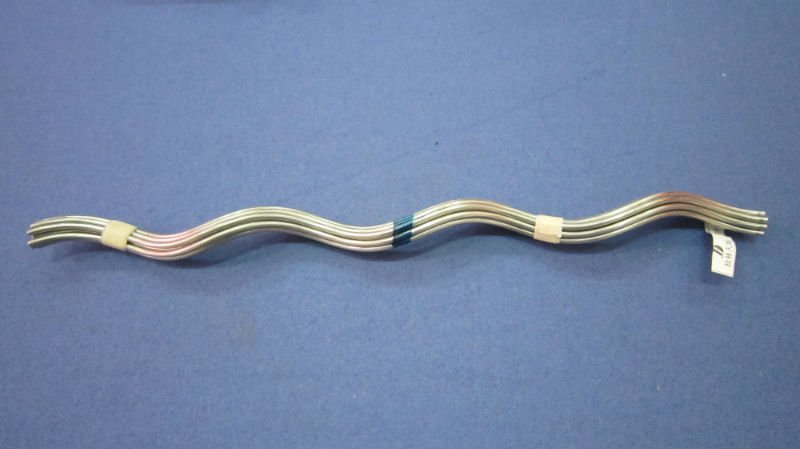
- Material – some materials offer higher costs for armor rods than others. Galvanized steel balance costs and performance. Price ranges between $1- $9 for ADSS cables depending on material.
- Size and quantity – thicker rods offer greater protection but are high at cost per unit. Length of armor rods impacts the total costs. Price ranges from $10 – $12 for sizes ranging from 0.390-0.413 inches.
- Installation method – hiring experienced technicians might be necessary for large projects.
- Special coatings – extra coatings such as paint to epoxy provide further protection against specific elements. This leads to higher costs for armor rods.
Frequently asked questions
An armor rods is a component used to provide mechanical protection to the conductor and enhance the grip between the conductor and the suspension clamp.
Armor rods serve to enhance the grip between the conductors and the clamps while providing mechanical protection against abrasion and wear. This ensures the stability and reliability of overhead transmission lines.
They prevent conductor sagging and reduce wear which contributes to the efficient power transmission and minimize power losses.
Armor rods are available in designs such as helical, double-helix and cross-armor configurations.